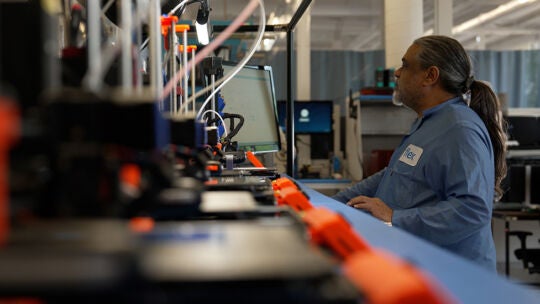
Mientras los fabricantes de todo el mundo se apresuran a digitalizar la planta de producción, Flex analiza la importancia de la digitalización y cómo extraer el máximo valor de los datos para generar resultados comerciales positivos.
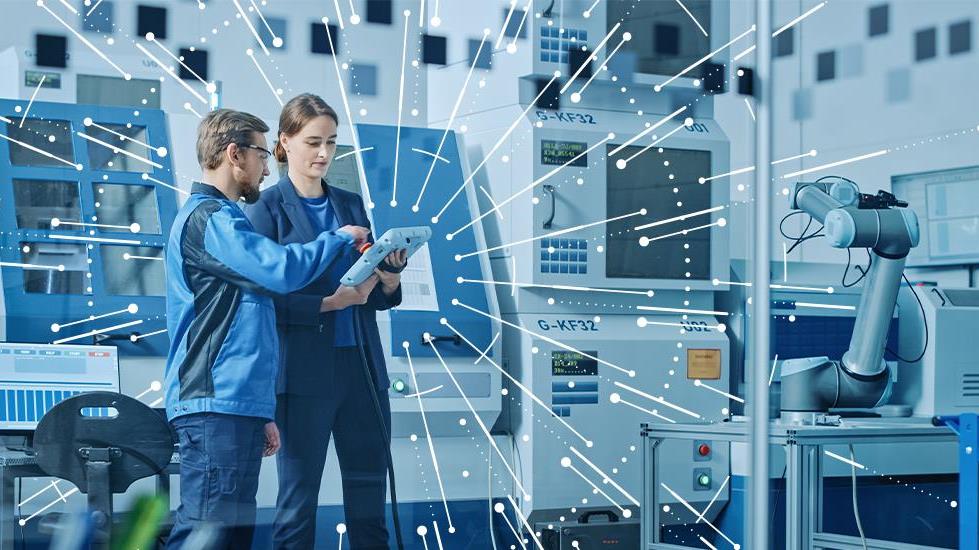
La pandemia mundial generó cambios masivos en la forma en que hacemos negocios. El año pasado puso de relieve las mejoras necesarias en las cadenas de suministro globales, puso a prueba la resiliencia de los procesos de fabricación y destacó la importancia crítica de la digitalización y los datos en el taller.
Por ejemplo, Flex produjo recientemente su mascarilla número 100 millones para nuestros empleados y sus familias. Cuando estábamos en las primeras etapas de la pandemia, digitalización aprovechada durante todo nuestro proceso de elaboración de mascarillas. Instalamos pantallas en diferentes fábricas que mostraban las mejores prácticas de cada sitio y aprovechamos la información de los dispositivos conectados para comprender cómo podríamos aumentar nuestro rendimiento. Como resultado, los técnicos del taller podían trabajar juntos en tiempo real a pesar de estar a miles de kilómetros de distancia. Con la digitalización, todo se vuelve mucho más rápido y en tiempo real.
Las inversiones que realizó Flex para digitalizar nuestra fábrica antes de la impredecible pandemia produjeron resultados tremendos. Sin embargo, aquellos que se quedaron rezagados en las iniciativas de transformación digital se apresuran a ponerse al día. De hecho, una reciente Informe sobre el estado de fabricación de 2021 mostró que 91% de los tomadores de decisiones de fabricación están aumentando sus inversiones en transformación digital este año.
Estas inversiones probablemente vendrán en forma de sensores del Internet industrial de las cosas (IIoT), dispositivos conectados y otras tecnologías inteligentes. Cuando se utilizan de forma eficaz, estas herramientas producen datos en tiempo real que aumentan la productividad, impulsan la eficiencia y permiten una toma de decisiones más inteligente y rápida.
Cuando se hace correctamente, la digitalización de una fábrica puede generar resultados increíbles, pero puede haber muchos obstáculos y comienzos en falso. Con operaciones de fabricación en más de 100 sitios que cubren más de 50 millones de pies cuadrados de espacio de fabricación en todo el mundo, hemos desarrollado varias mejores prácticas para transformar las plantas de producción.
No te pierdas en los conjuntos de datos
Una sola línea de producción puede generar más de 70 terabytes de datos por día, suficiente información para caber en cinco millones de guías telefónicas.
Es tentador explorar montañas de datos para encontrar una sección que parezca interesante o que pueda conducir a una mejora del proceso. Si bien la curiosidad puede llevar a algunos trabajadores a explorar con más detalle, normalmente no es una buena elección. En cambio, los datos son más beneficiosos cuando los empleados comienzan con un problema en mente.
La pregunta que todo equipo debería hacerse es: "¿Cómo me permiten los datos realizar cambios duraderos que beneficien al cliente desde una perspectiva de calidad, entrega a tiempo o producción?". Una vez que esa pregunta se solidifica, el análisis de los datos se vuelve más enfocado.
Desarrollar un plan de datos y digitalización
Los fabricantes deberían dedicar 30% del tiempo a pensar en cómo los datos pueden ayudar a resolver un problema específico, 30% del tiempo a descubrir dónde residen los datos para resolver ese problema, 30% del tiempo a impulsar mejoras basadas en esos nuevos datos y solo 10% del tiempo. tiempo en la implementación técnica. La atención debe centrarse siempre en encontrar formas de extraer información que ayude a impulsar la mejora empresarial.
Convierta los datos sin procesar en acción con capacitación
¿Y cómo se toman grandes cantidades de datos sin procesar y se convierten en información procesable? Gente. Uno de los aspectos más pasados por alto pero de importancia crítica en cualquier adopción de tecnología es la gente que aprovecha las herramientas. Esto es especialmente cierto cuando se trata de fabricación digitalizada.
No es suficiente gastar $10 millones en hardware y software si no inviertes en tu gente para que puedan operarlo con inteligencia. La capacitación se presenta en muchas formas, incluidos manuales paso a paso, capacitación en el trabajo donde los trabajadores pueden obtener experiencia práctica con interfaces de máquinas e incluso entornos simulados donde pueden trabajar en un entorno virtual sin poner en riesgo el tiempo de actividad de la línea.
También es fundamental que los programas de formación se centren en el pensamiento sistémico. Por ejemplo, si un empleado realiza cambios en una máquina, puede afectar negativamente al equipo en la línea y potencialmente interrumpir la producción posterior. Comprender el sistema completo es primordial.
Los datos en tiempo real necesitan decisiones en tiempo real
Durante la pandemia, muchos trabajadores de apoyo se vieron obligados a quedarse en casa y la gente en el taller era responsable de aprovechar los conocimientos de los procesos digitalizados. Dado que una fábrica es un ecosistema en constante movimiento, no es factible que los empleados en casa analicen datos y sugieran mejoras basadas en la información. Después del hecho no funciona en un entorno de fabricación.
Por eso es tan esencial democratizar el acceso a los datos y capacitar a cada empleado para que aproveche los conocimientos para impulsar un cambio significativo. Esto puede tener resultados poderosos y de gran alcance tanto para los clientes como para los procesos internos.
Los beneficios de una fábrica digitalizada y basada en datos
Cuando se hace correctamente, las organizaciones de fabricación pueden obtener muchos beneficios de los sistemas digitales en tiempo real implementados en la Industria 4.0. Las empresas no sólo pueden alinearse mejor con los clientes, acelerar y optimizar los procesos, sino que también pueden aprender y tomar medidas para optimizar la producción en el futuro con menos riesgo.
Mientras que las fábricas heredadas producían bienes, la fábrica conectada de hoy produce bienes y datos. Al fin y al cabo, lo que marcará la diferencia es la forma en que estas fábricas utilizan los datos para resolver problemas, capacitar a los empleados para tomar decisiones en tiempo real e impulsar cambios sostenibles para los clientes.
Continúe descubriendo el papel que tienen la digitalización, las prácticas sostenibles y otras tecnologías avanzadas en la industria manufacturera en general. Leer más