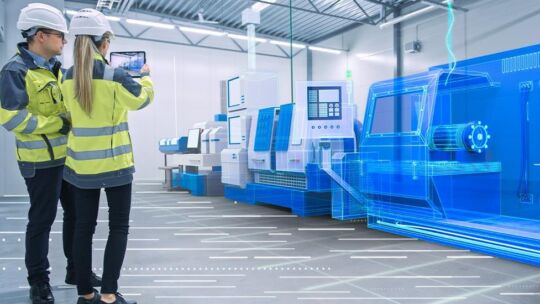
A medida que las ideas de productos se vuelven más complejas, los clientes buscan socios con capacidades avanzadas para ayudar a convertir conceptos en bienes tangibles de manera confiable, eficiente y rápida. Paul Baldassari de Flex comparte cómo la simulación juega un papel fundamental en este proceso.
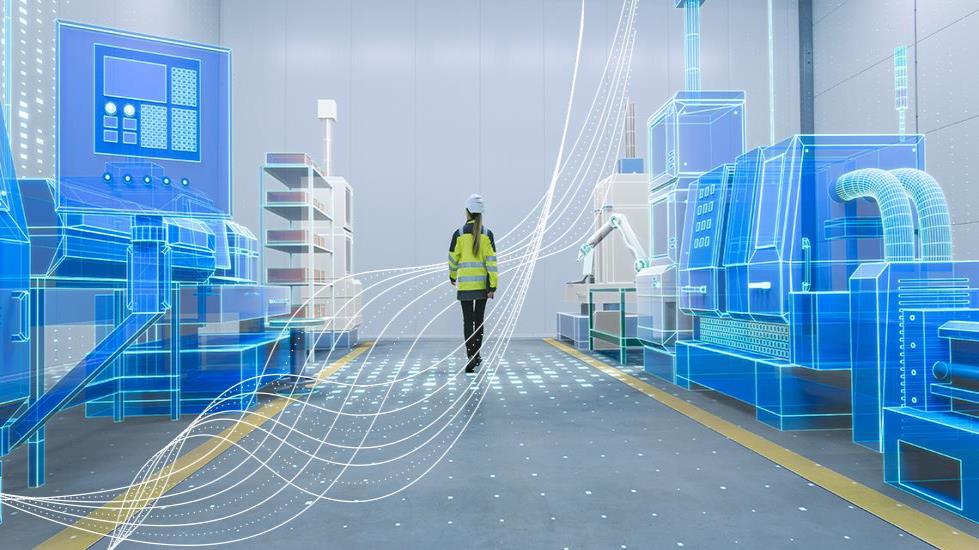
En una reciente Entrevista Forbes Al discutir el futuro de la fabricación, el director ejecutivo de Flex, Revathi Advaithi, compartió que "la industria está obsoleta en muchos sentidos". Incluso si miramos hacia atrás unos pocos años, hasta 2018, el porcentaje de corporaciones manufactureras que se transformaron con éxito fue mucho menor que el promedio 28% de empresas de otras industrias.
Este enfoque lento y resistente hacia la transformación digital, combinado con una mayor demanda de productos por parte de los consumidores y una pandemia global que generó importantes restricciones de viaje e interrupciones en la cadena de suministro, podría haber paralizado por completo la fabricación.
El futuro de la transformación digital en la fabricación debe centrarse en crear una cartera de tecnologías avanzadas que proporcionen mayor eficiencia, calidad y sostenibilidad a los clientes. Flex inició su transformación digital hace varios años. Resultó fundamental para afrontar la pandemia de COVID-19 y proporciona la flexibilidad para adaptarse a futuros cambios ambientales, globales e industriales.
Cuando la gente piensa en tecnologías de fabricación digital, es probable que lo primero que le viene a la mente sea la automatización y la robótica. Si bien son muy importantes, la única tecnología que en gran medida se ha pasado por alto pero que desempeña un papel esencial en la nueva era de la fabricación es simulación.
Los beneficios de la simulación
El poder de la simulación es que impulsa las conversaciones iniciales que necesita tener con los clientes, los socios de la cadena de suministro, los proveedores de equipos y los expertos internos antes de producir un producto.
- ¿Cómo se montará la fábrica?
- ¿Cómo fluirá el producto a través de la línea? ¿Hay áreas que se puedan optimizar ahora?
- ¿Cómo es el tiempo de rampa y cómo se pueden superar las expectativas del cliente?
- ¿Cómo es el rendimiento?
- ¿Cuántos empleados necesitamos para apoyar el proyecto?
- ¿Falta algo?
En el pasado, los clientes volaban a una fábrica para caminar por la planta y ver cómo salían los productos de las líneas. Si necesitaba cambiar una línea o configuración de fábrica, era un proceso manual laborioso que podía llevar meses. ¿Y si no fuera el cambio correcto? Estás de vuelta al punto de partida, volviendo a la configuración original, perdiendo tiempo y dinero.
He aquí por qué la simulación puede ser tan poderosa:
1. Comience virtualmente y luego hágalo de manera realista
Con la simulación, puede proporcionar una vista virtual de la fábrica para el cliente y los equipos internos. Esta vista puede mostrar cómo se ven las líneas e incluso resaltar la vista de la máquina. Si necesita realizar un cambio, con un simple clic estará ejecutando una nueva versión simulada.
2. Pruébalo antes de adoptarlo
También puede continuar creando y agregando capas lógicas con simulación. Una vez configurada la vista de línea, puede crear una vista simulada del flujo de material, equilibrar la línea y analizar el rendimiento del equipo. Puede hacer una predicción de rendimiento o simular lo que sucedería si una máquina o proceso no funciona según las expectativas. Una vez que tenga esa información, podrá abordar lo que significa una falla para todo su proceso de fabricación, las áreas que necesita corregir y las brechas en el rendimiento. Incluso puede simular la vista del inventario, asegurándose de tener el rendimiento adecuado sin crear una reserva considerable en la fábrica.
3. Visualice la experiencia de los empleados en la fábrica.
Otra cosa que ha resultado increíblemente útil es simular la visión de los empleados, especialmente durante la pandemia. Este proceso ayuda a comprender mejor la fábrica, cómo la gente utiliza los equipos y cuántos trabajadores se necesitan para un trabajo. Esta visión puede ayudar a garantizar que la fábrica esté diseñada de manera ergonómica para promover la seguridad y la eficiencia, al tiempo que previene lesiones y mantiene a los empleados socialmente distanciados.
4. El primer paso hacia el gemelo digital
La perspectiva de la fabricación es conectada, bidireccional y no sólo de bucle cerrado, sino de bucle correcto. La simulación sienta las bases para el funcionamiento de este sistema inteligente y actúa como el motor que impulsa la próxima generación de tecnologías de fabricación. Un modelo de simulación hoy es una representación de un proceso físico. En Flex, nos estamos embarcando en conectar lo físico y lo digital, creando un paradigma que permita una respuesta instantánea a preguntas comunes en la fábrica. Al combinar la simulación con otros sistemas de misión crítica, como la planificación de recursos empresariales (ERP), el sistema de ejecución de fabricación (MES) y más, el gemelo digital generará un entorno más eficiente. Los beneficios incluyen una mejor planificación de la producción, cambios de línea, fluctuaciones de la demanda de los clientes, soluciones para la escasez de materiales y otras variables que determinarán cómo superar mejor las expectativas de nuestros clientes.
Suscríbase a nuestro boletín para recibir las últimas noticias y recursos sobre Flex.
La creciente demanda de simulación
Inicialmente, la simulación se utilizó para probar nuevas configuraciones de línea o evaluar los beneficios de costos del uso de flujos de proceso alternativos. Sin embargo, nuevos avances están generando un cambio de percepción. De hecho, un encuesta reciente demostró que el 75% de los ejecutivos de fabricación creen que la simulación es fundamental para el éxito. Este cambio está impulsando un enorme crecimiento en el mercado, y se espera que el software de simulación llegue a más de $15 mil millones para 2026.
Sin embargo, sólo 43% de los ejecutivos de fabricación creen que sus capacidades de simulación actuales son buenas o excelentes.
Esto se debe a que integrar la simulación en cada faceta de su organización no es tan fácil como parece. La simulación requiere una estrecha colaboración entre múltiples departamentos, disciplinas y proveedores. La mayoría de las organizaciones de fabricación afirman confiar en la tecnología, pero en realidad solo la implementan para equipos y proyectos específicos. Como resultado, estas empresas no ven (ni transmiten) las ofertas de simulación de valor completo.
En Flex, tenemos una sólida herencia de reunir diferentes disciplinas para hacer bien los proyectos. nos hemos abrazado La simulación como piedra angular de nuestra iniciativa de fabricación avanzada. desde hace bastante tiempo. Al colaborar con los mejores de cada departamento, hemos completado más de 200 proyectos de simulación solo en los últimos dos años. Al integrar esta tecnología en el tejido de nuestros procesos, hemos incubado la experiencia necesaria para implementar esta tecnología en todas nuestras fábricas y expandir su uso y adopción rápidamente.
Entonces, ¿cómo se ve eso en la práctica?
Ayudar a los clientes con simulación: un ejemplo de dispositivo médico del mundo real
Como la mayoría de los mercados altamente regulados, el industria médica requiere una confiabilidad extremadamente alta durante todo el ciclo de vida del producto. Cualquier error o problema en el proceso de fabricación puede tardar años en solucionarse y costar millones de dólares en el proceso. Cuando Flex comenzó a trabajar con un proveedor de dispositivos médicos que buscaba lanzar un nuevo producto al mercado en 2020, sabíamos que la simulación desempeñaría un papel fundamental.
Con el poder de la simulación, pudimos reiterar el modelo del producto cientos de miles de veces en el transcurso de horas. Este proceso permitió a Flex ejecutar rápidamente escenarios hipotéticos y probar variables y restricciones. Utilizando la simulación, un método que de otro modo habría tardado tres meses en completarse manualmente, se completó en sólo tres semanas.
Pero ese no fue el único beneficio. El cliente también estaba trabajando contra demandas estrictas y necesitaba Flex para producir ocho millones de unidades por trimestre. Como sabe cualquiera en el campo, la programación de la producción siempre es un desafío. Los cronogramas, la demanda, las personas y los materiales siempre cambian y pueden causar un impacto significativo en los planes de producción. Como resultado, nuestro equipo predijo manualmente 5,5 millones de unidades por trimestre, muy por debajo de los requisitos del cliente. Sin embargo, al utilizar la simulación para probar varios escenarios, pudimos optimizar la programación en unos pocos días para producir 8,1 millones de unidades por trimestre (100.000 más de lo que esperaba el cliente).
Más allá del diseño y la programación, la simulación también ayudó a probar variables operativas importantes. Esto nos permitió aumentar la producción en algunas estaciones de trabajo en más de 70%, eliminar cuellos de botella y optimizar la disponibilidad de los carros en el taller en más de 20%, y ofrecer otros beneficios comerciales, operativos y de ahorro de costos esenciales. La simulación ayudó a dar vida rápidamente al dispositivo médico con los más altos niveles de calidad, confiabilidad y eficiencia.
Impulsando la próxima era de la fabricación
Hemos llegado a un punto de inflexión en la forma en que vemos la fabricación y existe una enorme oportunidad de crecimiento en la industria en un mundo pospandémico. En los últimos años, hemos demostrado que existe una mejor manera de hacer las cosas gracias a la simulación y otras tecnologías de fabricación avanzadas.
El cuarta revolución industrial Se trata de aprovechar la tecnología para construir mejores productos, y las iniciativas de fabricación avanzada seguirán brillando como un aspecto crítico que impulsa este movimiento hacia adelante. En 2020, nuestro equipo directivo utilizó ampliamente la simulación para mantenerse conectado con las fábricas. Junto con nuestros empleados y clientes, hemos estado recorriendo el taller virtualmente y tomando decisiones informadas basadas en datos y basadas en simulación durante todo el año.
La simulación ha desempeñado y seguirá desempeñando un papel fundamental a la hora de impulsar la próxima era de la fabricación. En mi próxima publicación, profundizaré en el Principales elementos a considerar al utilizar la simulación.