
En todo el mundo, Flex opera instalaciones que se especializan en fabricación de bajo volumen y alta combinación. Estos sitios producen cantidades relativamente pequeñas de una amplia gama de productos para médico, automotor, y aplicaciones industriales que tienden a ser complejos con requisitos de calidad específicos. A medida que la amplia combinación de productos se traduce en frecuentes cambios de producción, existe un tiempo de inactividad inevitable junto con la posibilidad de introducir errores cada vez que es necesario cambiar programas, procesos, materiales y herramientas para adaptarse a los cambios de producción.
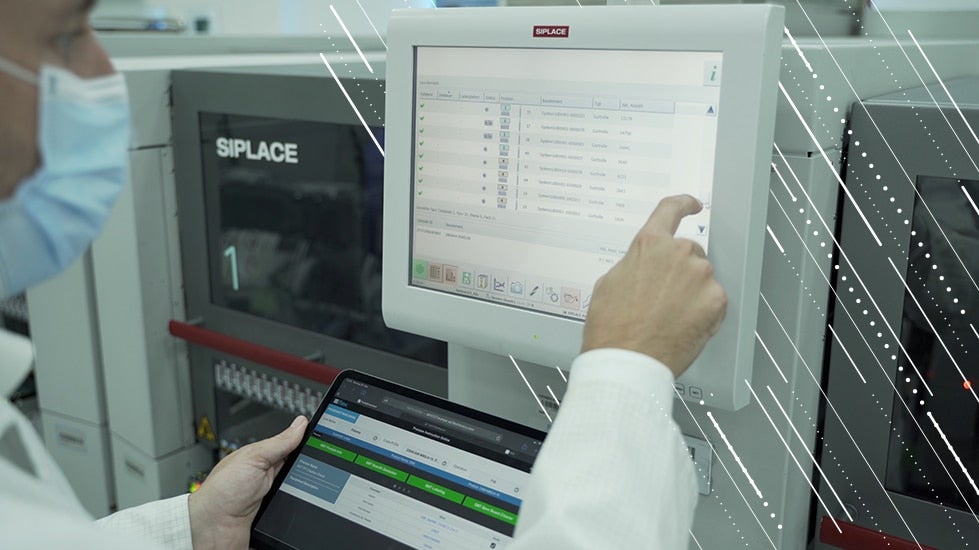
Presentando LISA
Flex Althofen en Austria es una instalación de bajo volumen y alta mezcla que atiende a más de 25 clientes con una cartera de más de 500 productos altamente complejos en lotes que van desde 100 a tres millones de unidades. Al fabricar más de 600 productos diferentes que van desde sistemas GPS para automóviles hasta dispositivos médicos de Clase III en un mes determinado, Flex Althofen registra un promedio mensual de 900 cambios de productos.
Como los cambios frecuentes y complejos del sitio eran parte de su rutina diaria, el equipo buscó mejorar la forma en que se gestionaban estos procesos. Inspirándose en el método de fabricación ajustada poka-yoke, o “a prueba de errores” en japonés, el equipo comenzó a desarrollar un asistente de parada de línea para minimizar los errores de cambio en enero de 2019.
El resultado fue LISA, un asistente de parada de línea 24 horas al día, 7 días a la semana, que tiene acceso en tiempo real a todas las fuentes de datos relacionadas con las líneas de producción.
Esta visibilidad permite a LISA realizar dos tareas:
- Detener líneas de producción mal configuradas, lo que hace que el equipo del taller resuelva el error.
- Evite que operadores no capacitados configuren líneas para las que no han sido capacitados
Vea LISA en acción:
Vídeo no disponible
El contenido que busca no está disponible en este momento. Agradecemos su paciencia y esperamos compartirlo pronto con usted.
LISA cumple
Antes de LISA, los miembros del equipo dependían de listas de verificación para configurar las líneas de ensamblaje y este proceso manual presentaba la posibilidad de errores que podrían aumentar los costos, el desperdicio y otras ineficiencias. Si alguien carga la receta incorrecta para un ensamblaje, por ejemplo, el resultado debía descartarse.
Desde el lanzamiento inicial de LISA en 2019, el sitio de Althofen ha experimentado mejoras en las métricas de cambio al reducir:
- Tiempo de cambio en un 10 por ciento
- Tiempo de limpieza de línea en un 85 por ciento
- El tiempo de inactividad relacionado con la calidad en un 56 por ciento
Otras mejoras incluyen:
- Aumento del 18 por ciento en la efectividad general del equipo (OEE)
- Los errores potenciales cayeron de ~900 a 0 por mes
- Reducción del estrés de los operadores
- Reducción del trabajo tedioso y repetitivo, liberando al personal para centrarse en trabajos de mayor valor.
LISA ha sido un recurso indispensable para ayudarnos a mejorar a pasos agigantados nuestros procesos de cambio y aliviar la presión de nuestros empleados. Desde que implementamos LISA, hemos seguido repitiéndolo y realizándole mejoras, para que nuestra fábrica pueda volverse aún más inteligente y eficiente.
— Martin Stefan, director de integración de fábrica, Flex Althofen