
No matter the stage of one’s career, an openness and passion for learning and mentorship is crucial to growth and success. This is especially true for three team members and their different experiences building a career in the manufacturing industry, where those who often succeed thrive in the excitement of learning new technologies, skills, cultures, and more.
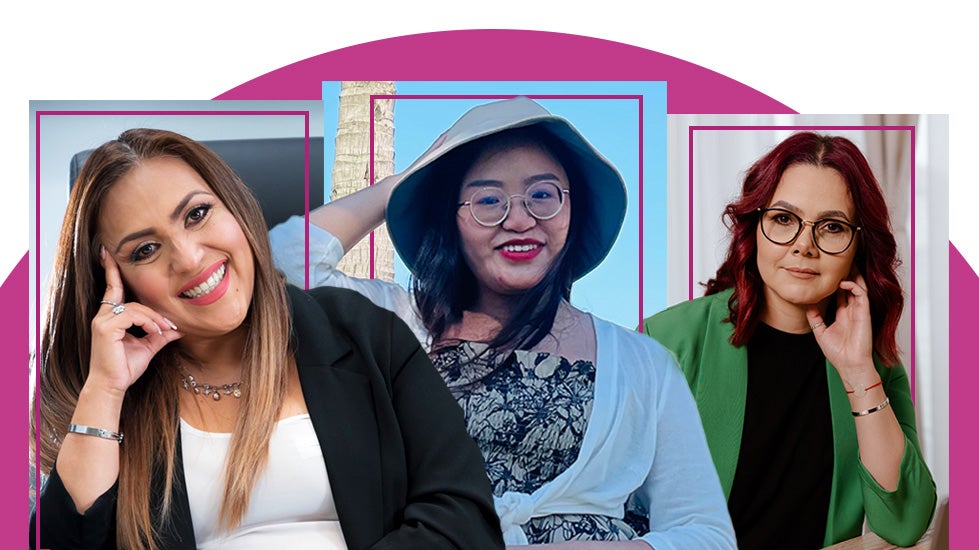
We caught up Tingting Zhen, a quality engineer in Zhuhai, China who started as an intern, Columba Garza, a senior director in program management and business development leader in Aguascalientes, Mexico who learned a new trade and aspires to grow her leadership even more, and Laura Vacarescu, a technical support manager with an extensive engineering background in Timisoara, Romania whose career spans several decades with the company. Check out excerpts from our conversations to learn how their professional journey has developed in manufacturing, and what excites them in their current role and beyond.
Tell us about the start of your journey at Flex and where you are today.
Tingting: I started at Flex in Zhuhai through an internship program in 2018 when I was a third-year student working on a bachelor’s degree in Business English. I received this degree to work in English-speaking companies but wasn’t exactly sure what role I wanted yet. Luckily, the Flex internship allowed me to explore different departments and I discovered my passion for quality engineering.
After completing my internship and graduating, I was excited to learn that there was an opportunity for me to interview for a full-time position. I was drawn to Flex for the exciting atmosphere, company culture, and the welcoming, accessible environment.
As a person with a disability, accessibility is very important to me. At Flex, I can access any building, including dormitories, by myself. I love that the company welcomes people of all types of disabilities, so I’m not alone.
Columba: My father had a career in mechanicals, so I’ve always been inspired by him to work in a similar industry like electronics. I started at Flex in finance, and, at first, it was very challenging because Flex is a fast-paced place with plenty to learn about how our sites operate. When starting, my main goal was simply to always do my best. Once I adapted and started excelling in my role, my goal was to be a leader.
My manager offered the opportunity to work with the vice president of finance for the Americas region, which expanded the scope of my work from one site to 130 at the time. This helped me build my skillset within corporate finance and learn how to manage expenses like capital expenditures. Now, I work as a senior director in program management and business development, using my finance skillset but I also interact with several other teams.
Laura: When I graduated high school, I knew I wanted to be in a technical role. Flex was one of the largest companies at the time and on another continent (North America), so I took on a challenge right from the very beginning, but I was excited to learn new things.
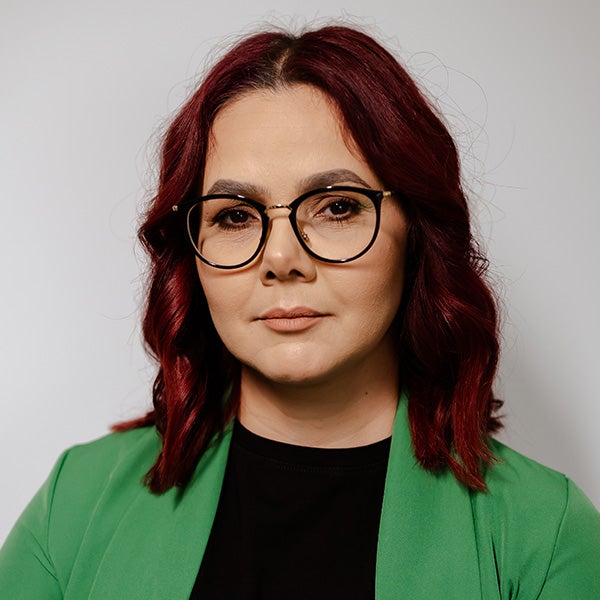
I’m so proud to be working with a company that’s recognized and admired, and where a culture of a collaboration is truly a differentiator. I started at Flex in 2000 as an operator – one of the first certified operators at the site to work with optical fibers.
— Laura Vacarescu, technical support manager
The optical fibers used in fiber optics are sometimes made of plastic but are often made of glass. In telecommunications, optical fibers have been used to replace copper wire in long distance telephone lines and are used to link computers within local area networks. As an operator, I helped maintain the specialized equipment and supervise the quality of materials produced.
I then progressed in several different engineering roles leading up to being a senior design for excellence (Dfx) engineer, specializing in optical manufacturing where I help design processes for better efficiency and higher quality material.
Optical assemblies include specialized process requirements such as cutting, cleaning, polishing, and splicing optical fibers. This is a very interesting and challenging task that ensures there will be no loss of signal or delays in data.
As an engineer, my day-to-day includes data analysis, ordering new tools for processes if necessary, and reporting out on issues and recommending design improvements. I even help prepare customer documentation for operators and train operators on the line. Recently, I went to one of our Guadalajara sites to provide support for training on optical fiber splicing and made recommendations for improvements.
Throughout your career, what has been the most impactful to your development so far?
Tingting: When I joined Flex, I trained through the Mechanicals School, a Flex training program in Zhuhai, where we have nine months to learn the departments and choose which one is the best fit. I chose to join quality assurance as a quality engineer because you quickly understand the operations of the entire company, since we test systems and procedures for all types of products and many different contexts.
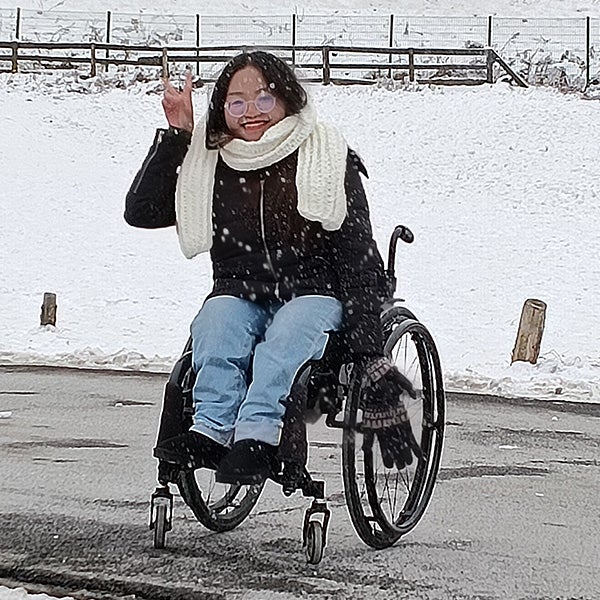
The internship program at Flex gave me the opportunity to learn about the company and decide it was the right fit for me as a student. The Mechanicals School provided me the knowledge I needed to be successful at work.
— Tingting Zhen, quality engineer
Columba: Mentorship is the best resource, both from my manager and my teams. They knew I was ready to grow and gave me the opportunity to do so. My manager helped me build the tools and confidence to go for it. Another resource is my team. I’m transparent about what my background is – finance and not engineering. And we help teach each other and support each other to reach organizational goals. My team is truly the best.
Laura: In 2006, Flex helped me get certified to work with optical fiber to learn the Design for Optical Assemblies (DFO) process, which kickstarted my career on the factory floor. For me, the certification was particularly useful since I learned more about the design and innovation side. Plus, I was one of the first employees to be certified. It was an honor for me to get this certification and I feel one of the best resources at Flex is working with the different subject matter experts, who are willing to help you learn.
What do you think is the most meaningful part of your work?
Tingting: My work helps the operations department identify problems and ensure that we pass audits, which I mainly do by reviewing documents and doing an annual review to ensure everything we document about products and processes is consistent with the actual operation. My work isn’t just technical. I also learn important skills like time management, skills-sharing, and negotiation which help me solve problems. At the end of the day, my role does all the quality checks necessary to ensure we meet customer needs and reduce overall risk.
Columba: I have six managers reporting into my organization with different areas of expertise. Together, we’re focused on New Product Introductions (NPIs) and the goal to grow and meet the customer needs. I love the opportunity to be on the front lines of this growth for our customers while growing my strategic skillset.
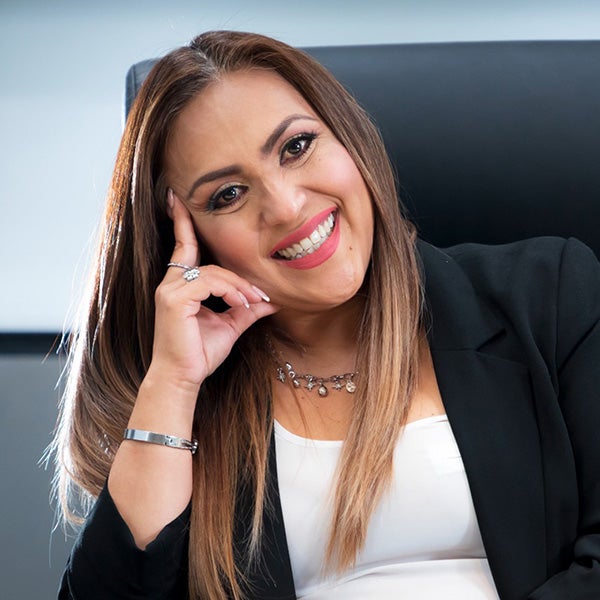
My favorite part of my job is when we get to work with a new customer since my team and I are dedicated to learning and taking on new challenges. It’s very satisfying to look back and say, we helped build and deliver products for our customers and played a part in the exciting growth. Since Aguascalientes is a zero-waste certified site, we’re proud to grow with sustainability in mind.
— Columba Garza, senior director in program management and business development leader
Laura: Fiber optical products have a unique material with a challenging manufacturing process since only an expert operator can run the process on the splicing team, where I specialize. I loved getting to learn how to solve different engineering problems on the factory floor. As I progressed into leadership roles, training became an area I had to learn quick. I’ve trained operators, I’ve trained staff to train, and I trained engineers!
Looking forward, what are you most excited about for the future of Flex?
Tingting: I look forward to continuing to develop my career here, since I still am early in my development and want to learn more. Right now, I’m learning more about the audit process which is interesting and a great way to learn a new aspect of quality of control. I also as a whole, am excited for the recruitment of all kinds of people with disabilities to get jobs in this exciting industry.
Columba: The continued growth in Aguascalientes is very exciting for me since it’s our job to make this growth a reality. We’re working on a strategic plan, and my goal is to help my team deliver, and ultimately, develop and prepare team members to eventually take my place.
Learning and development is critical to advancing my skills as a leader, and the same goes for my team. Great leaders recognize that prioritizing their teams’ development is a must for maximizing their impact for the business and doing right by their employees. And I’m excited to see how people-focused Flex culture is in terms of investing in employee health and happiness. When I close my office door, I am 100% a mom who’s dedicated to her family.
Laura: I was recently promoted from my senior engineering position into a Technical Support Manager (TSM) role. This is totally out of my comfort zone, but I am ready for the challenge since I’ll be working on projects with new technologies, new materials, and new equipment, and will also now involve production support, like the work I did in Guadalajara that I mentioned earlier.
Also, now I’ve started to work with sites outside of Timisoara to fix not only splicing and fiber optics, but also manufacturing, materials, testing, and processes in the industrial industry. I’m also learning more about robotics and automation. Luckily, being at Flex for so long gives me the advantage of at least being familiar with different technologies and industries, but I’m still learning a lot and look forward to learning more.
These stories of our Flex colleagues shine a light on the impact the people at Flex are making on manufacturing at all backgrounds and stages of career. Learn more about our commitments to our people who collaborate across the globe to create the extraordinary every day.