
Building a career engineering connected medical devices of the future
As the manufacturing partner of choice, we employ and develop the industry’s best makers, problem-solvers, and innovators who manage every step of the product, from design engineering to manufacturing, for a diverse range of industries.
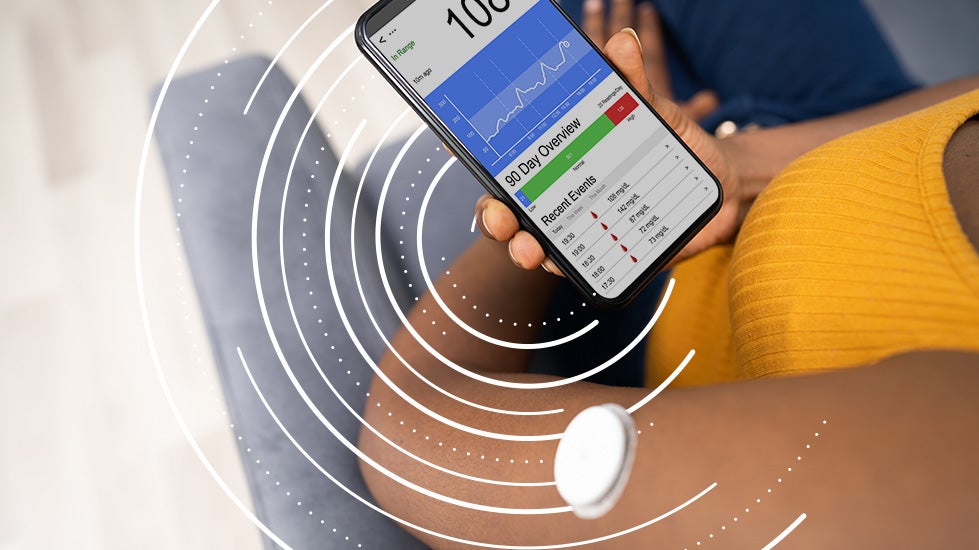
One of these industries is healthcare. With skilled teams and strong expertise in medical design and engineering, Flex has a deep understanding of the complex requirements for medical devices and collaborates with customers to solve their toughest design challenges. We deliver commercial medical devices that address user needs and transform patient care, including blood glucose monitors, autoinjectors, and wearable patch pumps.
To understand what it means to work in a medical design center developing these products, we caught up with Stefan Lovas, hardware development engineer, who joined Flex in 2018 as an intern at our design center in Timisoara, Romania.
Tell us about how you started at Flex at the Medical Design Center
My career at Flex started in the summer of 2018. As a third-year student at the Polytechnic University of Timisoara, Faculty of Electronics, Telecommunications, and Information Technologies, I was looking for an internship opportunity to complete my grade.
I went through several internship interviews and was offered an automotive product testing role at a different company, but I wasn’t sure whether that would be the best learning opportunity. As a young student, eager to learn, I was looking for an opportunity to make a real impact in people’s lives.
One of my professors told me about the Flex design center in Timisoara and how the local teams were looking for a hardware engineer trainee. A role at a design center focused on electrical medical device development and innovation was more appealing than product testing, so I took the leap, applied, and accepted this new challenge.
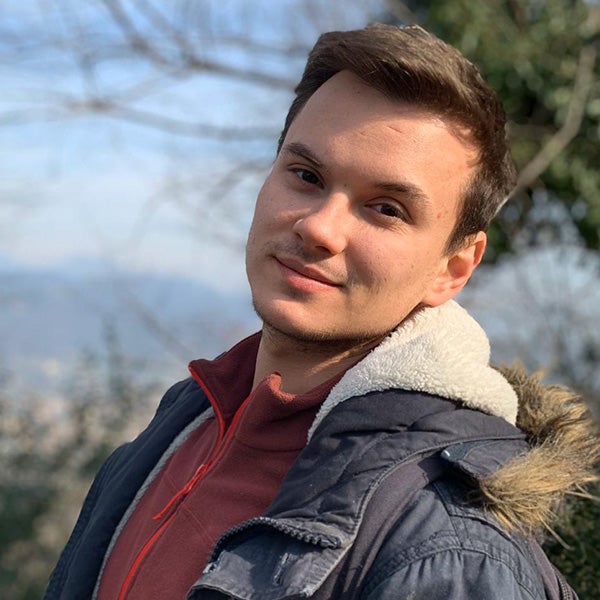
I am collaborating with a global network of engineers across Flex medical design centers and talented people who dedicate their time, skills, and experience to design and improve medical devices.
— Stefan Lovas, Hardware Development Engineer
When I joined the internship program, I didn’t have work experience, but I had a strong technical background and worked hard to improve my skills by collaborating with very talented people. Even today, the team is open to help, no matter how many questions you have, and is incredibly supportive of new joiners. The internship provided hands-on experience in using modern technologies and electronic equipment, such as digital oscilloscopes, signal generators, spectrum analyzers, battery testers, simulators, and others.
Following my internship, I was hired on as a full-time employee and four years later, I still think I made the right decision. Today, I’m happy to be a hardware development engineer within the Timisoara design center.
Can you elaborate on how your internship paved the way for designing medical devices?
This internship was my very first experience at an international company. I had a great time, working closely with talented engineers who taught me not just technical skills, but soft skills as well, like working in cross-functional teams. What stuck with me was seeing how many people from different backgrounds, cultures, and countries came together and collaborated to create a product that meets the customers’ needs with the goal of improving the life of the end users.
After my internship, my manager asked if I wanted to come back the following year to work on my graduation project called “The design of an invasive glucometer.” A glucometer is a meter that measures and displays the amount of sugar (glucose) in your blood that is often used by hospitals and individuals who are diabetic.
For this project, I built an electronic device that simulates how a real invasive glucometer works — transmitting glycemic (blood glucose) values through Bluetooth and eliminating the need to write data on a note-pad. In theory, this automation provides real-time access to data and leads to better treatment options for patients and more accurate records for doctors. By leveraging this data-transmitting protocol, my simulated device would offer access to real-time data on the mobile phone for the patient and doctor to help them make an informed decision regarding treatment.
This project helped me see the big picture of designing an electrical medical device and go through the many steps and stages involved. After thorough research, I started to create the electrical schematic, create a bill of material, develop a power budget, design the printed circuit board (PCB), and generate Gerber files (a standard to describe the printed circuit board images) to manufacture the PCB. I even had to manually solder the components, do electrical testing, write firmware to have basic functionalities, and finally, complete the documentation of the project.
When I graduated, I presented the project and product to a committee of university professors and won the award for best project of the year, a recognition I’m proud of. This project paved the way for my career as a hardware engineer for medical devices.
What type of electrical medical devices have you worked on?
I am pleased to say that my work has a positive impact in many customers’ products that are currently on the market and improving the quality of life for patients.
Diabetes is a serious disease affecting millions of people globally, and many of the products we work on are diabetes management systems, which allow patients to check glucose levels, and drug administration devices using technologies that enable real-time patient insights.
When you work in a medical design center and your work revolves around customers’ healthcare devices, the research and learning part never stops. You need to be on top of your game regarding all the latest developments in technology.
I collaborate with other team members — from supply chain engineers to sourcing engineers and quality, testing, or software engineering — to work on autoinjectors, wearable injectors and pumps, continuous blood glucose meters, and injection pens.
Can you walk us through the stages of an electrical medical device development process?
Every day is different, and the development process depends on the project and the stage reached in the design process. If the product we are working on is in the development stage and we need to create the electrical schematic or write the documentation, then our focus will be on research using datasheets and protocols to ensure that all parameters for electrical components are meeting customer and regulatory requirements.
The best days are when we’re in the early stages of designing a product with customers, especially when we test the electrical part and confirm that the paper-based analysis performed in the research stages is achievable. In this analysis, the documentation reveals a set of data which needs to be verified to make the product achievable in a real-life product scenario. Throughout this stage, we also check for any possible design flaws. This is where problem-solving skills come in handy, as we need to find solutions that improve the electrical settings of the product while managing costs and materials.
I like the early stages of designing a product very much because I feel like my work as a hardware development engineer is often like that of a detective trying to find the clues that will improve the product’s functionality.
Medical device development is a team effort as engineering teams must ensure that all their requirements are met, starting from the smallest piece to the shape and design of a product. We cannot design a device with the right hardware and software without meeting the mechanical engineering requirements. All the parts have to fit and work together flawlessly.
What would you recommend to a person looking to venture in the electrical medical device development space?
Besides a solid technical background, I would say perseverance and the will to constantly improve yourself and your soft skills, such as how to present results to the customer. Once you get a grasp on what electrical medical device development really means, you’ll rely more on thinking outside the box and realize that ideas come from anywhere, anyhow.
I would also say it does help to have a good sense of humor. Because humor opens the door to communicating easier with people, especially when you are working in a cross-functional team across different countries and cultures.
Speaking of teams, I work in a tight-knit team with a solid technical background, and I constantly learn from my colleagues. As a hardware development engineer in the Timisoara Design Center, I work with the latest technologies in my field and collaborate with colleagues from Milan and Althofen, growing my skills and expertise with each new product and work trip.
Whether you join Flex as an intern or you are an experienced professional, once onboarded, you’re on an accelerated learning and development path to succeed in your role.