
Energiespeichersysteme (ESS) spielen bereits eine wichtige Rolle in Stromnetzen. Sie sind eine Backup-Ressource, um Schwankungen in Stromnetzen zu bewältigen oder als Speicher für erneuerbare Energie zu dienen, die später in das Stromnetz eingespeist wird. ESS wandeln sich von einer unterstützenden Rolle zur Hauptbühne für ein besseres Netzmanagement für viele Versorgungsunternehmen.
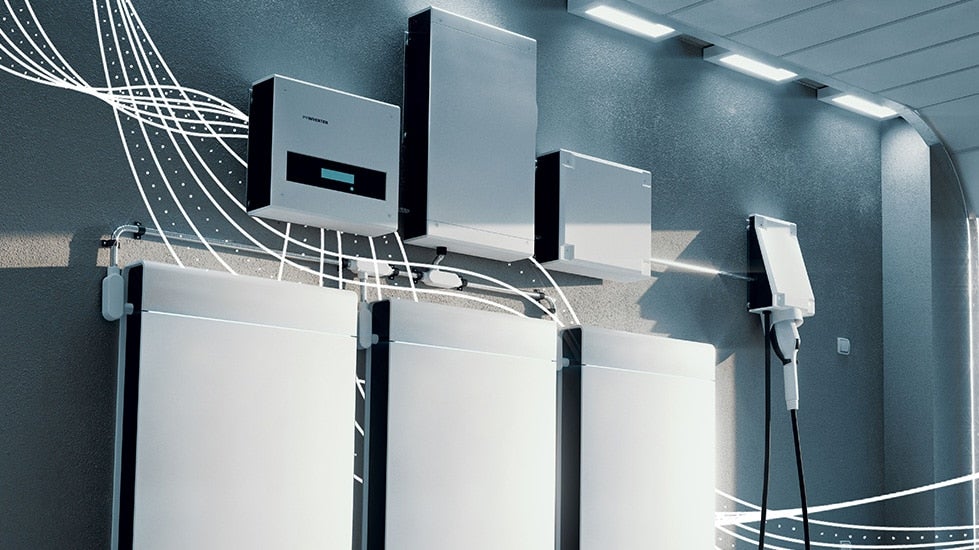
Eine weitere Aufgabe von ESS ist die Unterstützung der wachsenden Infrastruktur für private und gewerbliche Ladestationen für Elektrofahrzeuge. Die schnelle Akzeptanzrate von elektrische Fahrzeuge (EVs) treibt das Wachstum von Schnellladestationen voran, für deren Stromversorgung nicht nur das Stromnetz, sondern auch Energiespeichersysteme erforderlich sind. Ladestationen für Elektrofahrzeuge mit ESS machen das Laden kostengünstiger, indem sie in Zeiten geringer Nachfrage Energie aus dem Netz beziehen und in Zeiten der Spitzennachfrage Strom zum Laden von Elektrofahrzeugen abgeben.
Europa ist derzeit führend und verfügt über die meisten ESS als Teil seiner Stromnetzinfrastruktur. Laut einer Studie vom Februar 2020 gehören Nordamerika, China und Indien zu schnell wachsenden Märkten, die durch staatliche Anreize zum Netzausbau, die Abhängigkeit von erneuerbaren Energien und die gestiegene Nachfrage nach Elektrofahrzeugen angetrieben werden MarketsandMarkets-Bericht.
Was sind Energiespeichersysteme?
Einfach ausgedrückt ist ESS die Erfassung der einmal erzeugten Energie zur späteren Nutzung, um eine stetige Energieversorgung aufrechtzuerhalten. Diese Systeme bestehen aus interner Elektronik, AC/DC-Panels, Wechselrichtern, HVAC-Systemen, Betriebssoftware/-hardware, Batteriemodulen, einem Wärmemanagementsystem und einem Feuerlöschsystem. Ein typisches System befüllt einen eigenständigen Metallbehälter und wird zur Unterstützung eines Vorgangs an seinen Platz gebracht. Die Metallbehälter können klein genug sein, um an der Garagenwand eines Privathauses zu hängen, oder so groß wie ein Versandcontainer. Mehrere Speichersysteme können miteinander verbunden und von einem Steuerungssystem betrieben werden, um den Energiefluss für das Netzsystem zu steuern, oder als eigenständiges System fungieren, das mit Solar- oder Windkraft betrieben wird.
Welche Batterien sind die beste Wahl für ESS?
Moderne ESS gehen in den Batteriemodulen weg von herkömmlichen Blei-Säure-Batterien hin zu Alternativen mit höherer Energiedichte, höherer Leistungsdichte, längerer Zyklenlebensdauer und längerer Kalenderlebensdauer. Da die Preise gesunken sind, sind Lithium-Ionen-Batteriemodule zu einer attraktiven Option für den Einsatz in ESS geworden.
Um Ihnen bei der Auswahl der am besten geeigneten Lithium-Ionen-Zellen für die Erstellung des Batteriemoduls für Ihr ESS zu helfen, kann Ihnen das Flex Advanced Battery Systems Team (Batterieteam) behilflich sein. Wir verfügen über ein tiefes Verständnis der Zelltypen, der Zellchemie, der Anwendungsanforderungen sowie der internen Leistungscharakterisierung und Alterungsbewertungen, die für alle mechanischen und elektrischen Anforderungen die beste Lösung bieten.
Aufbau eines zuverlässigen ESS
Wie oben erwähnt, ist die Liste der Komponenten für ESS kurz, aber der Erfolg des Systems hängt von der Herstellung langlebiger, zuverlässiger Batteriemodule ab. Ein Batteriemodul ist eine Gruppe identischer einzelner elektrochemischer Zellen, die parallel und anschließend in Reihe geschaltet sind, um die gewünschte Spannung, Kapazität oder Leistungsdichte bereitzustellen.
Es gibt drei Möglichkeiten der Zellverpackung, die zur Herstellung eines typischen Batteriemoduls verwendet werden.
- Zylindrische Zelle
Diese Zelle ist das, woran die meisten Leute bei einer Batterie denken. Bei einer typischen AA-Batterie handelt es sich um eine einzelne Zelle, die im privaten, gewerblichen und industriellen Bereich eingesetzt wird. Die Zelle entsteht durch das Aufrollen blechartiger Anoden, Separatoren und Kathoden und wird in zylinderförmige Behälter verpackt.
Dieser Batterietyp ist am beliebtesten, da er kostengünstig und einfach herzustellen ist. Ein weiterer Vorteil der zylindrischen Form besteht darin, dass der Innendruck durch Nebenreaktionen gleichmäßig verteilt werden kann. - Prismatische Zelle
Diese Zelle entsteht durch die Schichtung der plattenförmigen Anoden, Separatoren und Kathoden in einem rechteckigen Metall- oder Hartplastikgehäuse. Das Design der Zelle verbessert die Raumausnutzung und ermöglicht eine flexible Gestaltung.
Da sich die Industrie in Richtung Elektrifizierung verlagert, werden diese Zellen in Batteriepakete für Elektrofahrzeuge, Energiespeichersysteme und andere Hochleistungsanwendungen eingebaut. - Beutelzelle
Für einen minimalistischen Verpackungsansatz sind die Zellen in flexibler Folie verpackt; Sie sind leicht und lassen sich problemlos in jeden verfügbaren Raum eines bestimmten Produkts einbauen.
Diese Batterien werden aufgrund ihrer Vielseitigkeit täglich in immer mehr Anwendungen eingesetzt, müssen jedoch aufgrund ihrer nicht starren Verpackung sorgfältig gehandhabt werden.
Herstellung langlebiger Lithium-Ionen-Batteriemodule
Der Modulherstellungsprozess wird durch die Art der Batteriezellen bestimmt, die zur Herstellung der Batteriemodule verwendet werden, um eine Anwendungsspezifikation zu erfüllen. Und der beste Weg, Lithium-Ionen-Batteriemodule herzustellen, ist eine automatisierte Fertigungslinie, die auf einem Laserschweißsystem basiert.
Beispielsweise beginnt die Herstellung von Modulen mit zylindrischen Zellen mit dem Scannen und Einbau einzelner Zellen in einen starren Zellhalter, um die Zellen an Ort und Stelle zu halten. Nachdem die zylindrischen Zellen in die Modulhalter geladen wurden, werden die Batterielaschen für den elektrischen Anschluss über die Oberseite gelegt und per Laser verschweißt. Flex nutzt automatisierte Präzisionslaserschweißsysteme, um die Metalllaschen über die Zellen zu schweißen und diese zu verbinden. Dies sorgt für eine bessere Wiederholbarkeit, verbessert den Durchsatz im Vergleich zum mechanischen Punktschweißen und verringert das Risiko einer Zellpunktion.
Während der Verarbeitung auf den automatisierten Linien werden die Module abgeglichen, auf Spannung geprüft und nach dem Schweißen auf Laschenwiderstand überprüft. Alle diese Qualitätsprüfungen stellen sicher, dass das Modul zuverlässig und voll funktionsfähig ist, bevor die restlichen elektrischen und internen Komponenten, Software, Hardware und das Metallgehäuse hinzugefügt werden.
Der Herstellungsprozess für prismatische Zellen und Pouch-Zellen ist ähnlich. Die einzelnen Batteriezellen werden gescannt und getestet, bevor sie übereinander oder nebeneinander gestapelt werden. Sobald die vorgegebene Anzahl an Zellen vorhanden ist, werden die Endplatte und die Seitenplatten zum Modul hinzugefügt und per Laser verschweißt. Beim Laserschweißen kann das Schlackenmaterial präzise aufgetragen werden, um zu verhindern, dass die Schweißnähte zu groß werden und die Endabmessungen des Moduls verändern.
Der nächste Schritt ist das Anbringen der Sammelschiene, einer Metallschiene mit niedrigem Widerstand, um alle positiven und negativen Enden der Zellen zu verbinden, die wiederum mittels Laserschweißen befestigt wird. Die Stromschiene dient der Stromverteilung während der Nutzung des Moduls. Das Schlackematerial muss gleichmäßig aufgetragen werden, um Lücken zu minimieren, die zu einem Leistungsverlust oder einer langsamen Energieübertragung führen können. Die Präzision des Laserschweißens trägt dazu bei, eine maximale Verbindungseffizienz zu erreichen.
Bevor die Gehäuseoberseite montiert wird, durchläuft das Batteriemodul mehrere Tests, um sicherzustellen, dass es alle Anforderungen erfüllt. Sobald das Modul alle Qualitätsprüfungen bestanden hat, wird die Gehäuseoberseite angebracht und das fertige Batteriemodul wird zur Endprüfung weitergeleitet.
Wir verfügen über regionale Produktionsstandorte mit speziellen Automatisierungslinien für Batteriemodule und Präzisionslaserschweißmöglichkeiten. Diese Standorte verfügen bereits über Erfahrung in der Handhabung und Lagerung von Batteriezellen, um Sicherheits- und Umweltanforderungen zu erfüllen. Erfahren Sie mehr über unsere fortschrittlichen Fertigungskapazitäten Hier.
Nutzen Sie unsere globalen Ressourcen für Ihr nächstes ESS-Projekt
Nachdem wir gemeinsam mit Ihnen die geeignete Batteriezelle für Ihr Batteriemodul identifiziert und den Herstellungsprozess abgeschlossen haben, können wir Ihnen beim Aufbau des restlichen ESS helfen. Die HVAC-Regler, AC/DC-Panels, Wechselrichter, elektronischen Komponenten, das Wärmemanagementsystem sowie die manipulationssicheren und umweltfreundlichen Metallgehäuse können intern hergestellt oder von anderen Flex-Produktionsstandorten geliefert werden, um sicherzustellen, dass für Ihr Produkt hochwertige Komponenten verwendet werden. Wir haben Zugang zu regionalen und globalen Anbietern, die Sie bei der Beschaffung von Brandbekämpfungssystemen zur Vervollständigung Ihres Systems unterstützen. Schließlich verfügen wir über die Ressourcen und das technische Fachwissen, um Ihr System von Grund auf zusammenzubauen und das gesamte System einer Qualitätsprüfung zu unterziehen, bevor wir es an Ihren Kunden senden.
Wir bieten Lösungen für Ihr ESS
Wir können Ihnen beim Entwurf und Bau eines neuen ESS helfen oder Ihre bestehenden Systeme aktualisieren, um der wachsenden Nachfrage nach Elektrifizierung gerecht zu werden industrielle Anwendungen. Die automatisierten Fertigungslinien mit Laserschweißfunktionen montieren effizient Batteriemodule für Ihr ESS. Unser integrierter Fertigungsansatz vereint Komponenten, die in unseren erstklassigen Anlagen zusammengebaut werden. Das Endprodukt verwandelt Ihr ESS von einer unterstützenden Rolle in eine führende Rolle für Sie und Ihre Kunden.
Kontaktieren Sie uns, um mehr über die Entwicklung und Herstellung Ihres nächsten ESS zu erfahren.