
Die Herausforderung
Ein neuartiger Audiolautsprecher auf Basis der MEMS-Technologie soll das Audioerlebnis für Musikliebhaber, Gamer und Nutzer interaktiver Augmented-Reality-Erlebnisse revolutionieren. USound, ein österreichisches Start-up, wurde 2012 gegründet. Sie entwickelten einen Prototyp eines mikroelektromechanischen Systems (MEMS) für miniaturisierte Lautsprecher, das Benutzern ein immersives 3D-Audioerlebnis bieten sollte. Bis 2015 hatten sie mehrere Prototypen im eigenen Haus getestet und waren bereit, einen Fertigungspartner für die Skalierung der Produktion zu finden.
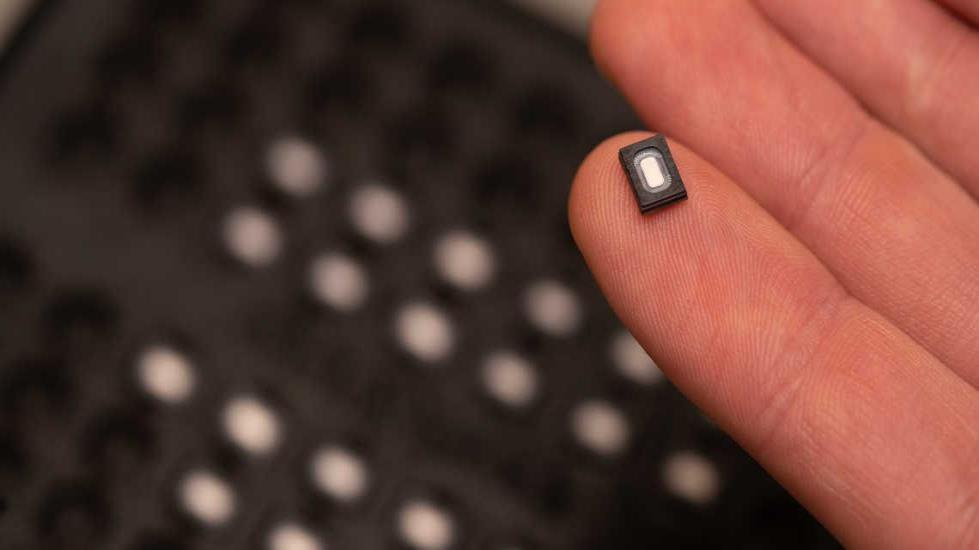
Design für die Fertigung
Ferruccio Bottoni, Mitbegründer und Geschäftsführer von USound, beschreibt ihre Position: „Als Neuling im Audiobereich haben wir uns stark auf das Design und die Entwicklung unseres Prototypprodukts mit dem Fraunhofer-Institut in Berlin konzentriert.“
Wir waren bereit, die nächste Stufe zu erreichen und unsere Fertigung an einen Dritten auszulagern, mussten aber einen Partner mit globalen Fähigkeiten finden, der aber auch vor Ort präsent war.
Ein gemeinsamer Lieferant schlug vor, dass wir mit dem Flex-Team in seinem Produktinnovationszentrum in Österreich sprechen würden, wo wir Zugang zu Expertenwissen in den Bereichen Design für Fertigung und Lieferkettenmanagement hätten.
— Ferruccio Bottoni, Mitbegründer und Geschäftsführer, USound
Strukturierte Methodik
Berthold Jaeger, Director of Business Development bei Flex in Althofen, war Teil des Teams, das sich mit USound traf:
Sie kamen mit einer brandneuen Technologie zu uns, die wir zuvor noch nicht hergestellt hatten. Das Prototyp-Design musste sorgfältig getestet und verfeinert werden, um sicherzustellen, dass das endgültige Massenprodukt stabil und von hoher Qualität ist. Unser systematischer Ansatz stellt sicher, dass das Design ausgereift genug ist, um in großen Stückzahlen hergestellt zu werden.
Die Lösung
Im April 2016 wurde USound mit dem „Produktinnovationszentrumsansatz“, wie Berthold es nennt, belohnt. Dadurch erhält ein neuer Kunde Zugang zu Spezialisten für Technologie, Design, Konstruktion und Fertigung in einem Team unter einem Dach.
Zusammenarbeit für die Industrialisierung
Der Standort Althofen ermöglichte es beiden Parteien, als ein einziges Team zu arbeiten, das dieselbe Sprache sprach und in derselben Zeitzone agierte. Der geografische Nähe der beiden Unternehmen sorgten für eine kontinuierliche Kommunikation und führten zu einer intensiven Zusammenarbeit. Dadurch konnten Materialien schnell getestet, ausgewählt und gekauft werden, während das Produktdesign verfeinert wurde.
Laut Bottoni war die Zusammenarbeit der Schlüssel zum reibungslosen Übergang vom Prototyp bis zur Markteinführung des Endprodukts. Die erste Phase begann mit der Analyse des „Laborprobenstatus“-Produkts durch das Flex-Team, um etwaige Schwachstellen im Hinblick auf die Industrialisierung zu identifizieren. Dies floss auch in die endgültige Stückliste und den Produktionsprozess ein.
Komplette Dienstleistungen für den Produktlebenszyklus
Berthold fährt fort: „Unsere Herangehensweise an Design und Technik Die von uns geleitete Fertigung und das Wissen über Fertigungstechnologien und Komponentenmaterialien halfen uns dabei, Designverbesserungen für das Produkt von USound vorzunehmen, um sicherzustellen, dass es für die Herstellung bereit war.
Zeit maximieren
Während die Analyse- und Planungsphasen mehrere Monate in Anspruch nahmen, konnte USound durch die Investition in einen strukturierten Ansatz vermeiden, dass die Produktion überstürzt begann, nur um später im Prozess noch einmal Fehler zu korrigieren.
Die Erfahrung zeigt uns, dass man hier viel Zeit und Geld verschwenden kann.
— Berthold Jaeger, Leiter Geschäftsentwicklung, Flex
USound und Flex erkannten, dass die Mikronatur der MEMS-Technologie eine vollautomatische Produktionslinie für die Lautsprecher erforderte. Das Flex-Team empfahl außerdem den Aufbau der Komponenten in Untergruppen, um den Herstellungsprozess zu vereinfachen. „Da diese Einheiten beispielsweise so klein sind, können die Teile nicht zusammengeschweißt werden, sondern müssen mit Klebstoff befestigt werden. Der Kleber wird in Nanolitern – sehr, sehr kleinen Punkten – aufgetragen, daher wurden spezielle Maschinen und Geräte angeschafft, um die Produktionslinie zu automatisieren“, erklärt Berthold.
Die wechselseitige Kommunikation spielte eine große Rolle dabei, sicherzustellen, dass alle Parteien über die Fortschritte informiert waren, und zwar durch tägliche Anrufe zwischen den Teams, monatliche persönliche Besprechungen und vierteljährliche Management-Updates.
Gewonnene Erkenntnisse
Mein Rat an jedes Start-up, das den Industrialisierungsprozess durchläuft, ist, sofort eine spezielle technische Ressource zu benennen, die mit dem Fertigungsteam interagiert und, wenn möglich, täglich vor Ort ist.
Kommunikation ist der Schlüssel, und der offene und kooperative Ansatz von Flex bedeutete, dass unsere Erwartungen erfüllt und Probleme zeitnah angegangen wurden.
– Ferruccio Bottoni
Das Ergebnis
Der Flex-Ansatz zur Verfeinerung und Entwicklung eines Prototyps bot USound eine Vorlage für die eigene interne Struktur, als sie ihr Team erweiterten. Als beispielsweise Flex von USound die Meinung eines Experten zu einem Bereich wie Beschaffung oder Qualität einholte, rekrutierte USound die Stelle. Durch die Nachahmung des Flex-Prozesses und die Sicherstellung, dass die erforderlichen Ressourcen intern vorhanden waren, konnte USound seine Mitarbeiter- und Wissensbasis erweitern.
Die Mengen wachsen
Nach Testläufen im November 2018 lief die erste serienmäßig produzierte Charge von Einheiten vom automatisierten Montageband. USound baut seine Produktion von monatlich 10.000 auf 20.000 Einheiten aus und plant, die Produktion im Jahr 2019 auf mehr als 500.000 Einheiten und im Jahr 2020 auf mehr als eine Million Einheiten zu steigern. Zusätzlich zur Fertigung verwaltete Flex die Lieferkette und Stücklisten für eingehende Komponenten von USound. Es ist geplant, auch die Ausgangslogistik für Original Design Manufacturing (ODM)-Kunden in China und China zu verwalten andere Standorte auf der ganzen Welt.
Ferruccio sagt: „Die Zusammenarbeit mit einem Multi-Milliarden-Dollar-Unternehmen hat dazu geführt, dass die endgültige Stückliste für unsere miniaturisierten Lautsprecher ganz anders war als die, die wir hatten, als wir Flex im Jahr 2015 zum ersten Mal trafen!“ Durch den Zugang zu einem globalen Komponentenmarkt, Produktionsanlagen und einem Netzwerk für Weiterlieferungen können wir unsere Ambitionen, ein österreichisches Fabless-Unternehmen mit internationaler Reichweite zu sein, verwirklichen.“
Etwas Licht im Ton
Die MEMS-Technologie von USound gilt als die Zukunft des Audios und wurde mit den Auswirkungen von LED-Lampen auf den Glühbirnenmarkt verglichen. Das Design der nächsten Generation befindet sich bereits in der Entwicklung, nachdem das Unternehmen eine zusätzliche Eigenkapitaltranche erhalten hat, die die letzte Finanzierungsrunde auf $30M erhöht.
Flex hat es uns ermöglicht, qualitativ hochwertige Produkte in großen Stückzahlen herzustellen und diese an unsere Endkunden zu vertreiben, sodass wir uns auf Forschung und Entwicklung sowie Vertrieb und Marketing konzentrieren können.
Wir planen, auch in Zukunft mit Flex zusammenzuarbeiten, nicht nur an unserer aktuellen Produktpalette, sondern auch an neuen Innovationen in der 3D-Audiotechnologie.
– Ferruccio Bottoni