
Überall auf der Welt betreibt Flex Anlagen, die auf die Herstellung von hochdiversen Kleinserien spezialisiert sind. Diese Standorte produzieren relativ kleine Mengen breit gefächerter Produkte für medizinisch, Automobilund Produkte für ein industrielle Anwendungen die in der Regel komplex sind und spezifische Qualitätsanforderungen haben. Da der breite Produktmix häufige Produktionsumstellungen mit sich bringt, kommt es unvermeidlich zu Ausfallzeiten und es besteht die Gefahr von Fehlern, wenn Programme, Prozesse, Materialien und Werkzeuge geändert werden müssen, um Produktionsverschiebungen zu berücksichtigen.
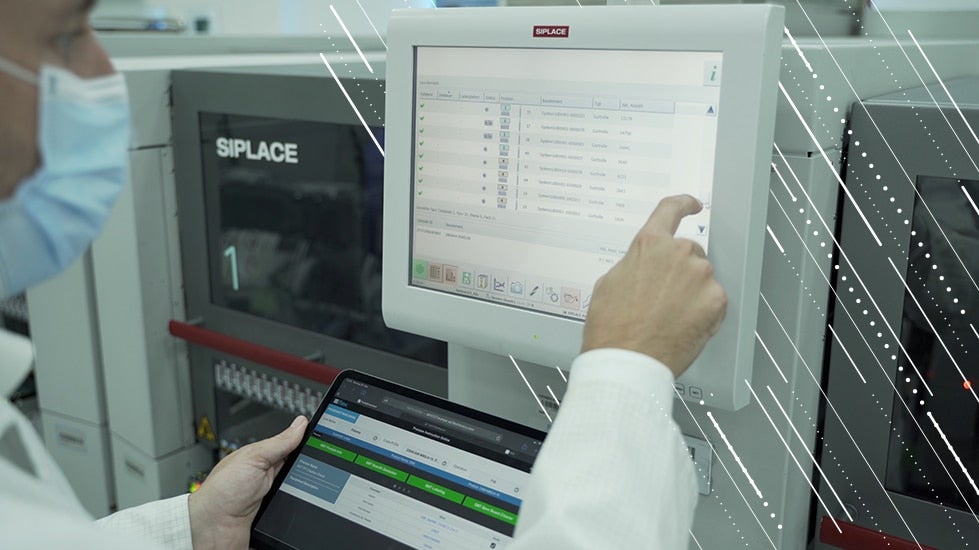
Wir stellen vor: LISA
Flex Althofen in Österreich ist ein Werk mit hoher Produktvielfalt und geringem Produktionsvolumen, das mehr als 25 Kunden mit einem Portfolio von über 500 hochkomplexen Produkten in Losgrößen von 100 bis drei Millionen Einheiten bedient. Flex Althofen fertigt jeden Monat mehr als 600 verschiedene Produkte, von GPS-Systemen für Autos bis hin zu medizinischen Geräten der Klasse III, und verzeichnet dabei durchschnittlich 900 Produktwechsel pro Monat.
Da häufige, komplexe Umstellungen zum Alltag des Standorts gehörten, wollte das Team die Verwaltung dieser Prozesse verbessern. Inspiriert von der Poka-Yoke-Methode der schlanken Fertigung (auf Japanisch „Fehlervermeidung“) begann das Team im Januar 2019 mit der Entwicklung eines Linienstoppassistenten, um Umstellungsfehler zu minimieren.
Das Ergebnis war LISA, ein rund um die Uhr verfügbarer Line Stop Assistant, der in Echtzeit auf alle Datenquellen der Produktionslinien zugreift.
Diese Transparenz ermöglicht es LISA, zwei Aufgaben zu erfüllen:
- Stoppen Sie falsch konfigurierte Produktionslinien und veranlassen Sie das Fertigungsteam, den Fehler zu beheben.
- Verhindern Sie, dass ungeschulte Bediener Leitungen konfigurieren, für deren Handhabung sie nicht geschult sind.
Sehen Sie LISA in Aktion:
Video nicht verfügbar
Der gesuchte Inhalt ist momentan nicht verfügbar. Wir danken Ihnen für Ihre Geduld und freuen uns darauf, ihn bald mit Ihnen zu teilen.
LISA liefert
Vor LISA verließen sich die Teammitglieder beim Einrichten der Montagelinien auf Checklisten. Dieser manuelle Prozess barg ein hohes Fehlerpotenzial, das Kosten, Abfall und andere Ineffizienzen nach sich ziehen konnte. Wenn beispielsweise jemand das falsche Rezept für eine Montage lädt, musste das Ergebnis verschrottet werden.
Seit der ersten Einführung von LISA im Jahr 2019 konnten am Standort Althofen die Umstellungskennzahlen verbessert werden, indem folgende Punkte reduziert wurden:
- Umrüstzeit um 10 Prozent
- Linienräumzeit um 85 Prozent
- Qualitätsbedingte Ausfallzeiten um 56 Prozent
Weitere Verbesserungen sind:
- 18 Prozent Steigerung der Gesamtanlageneffektivität (OEE)
- Potentielle Fehler sanken von ~900 auf 0 pro Monat
- Reduzierte Belastung der Bediener
- Reduzierung langwieriger und sich wiederholender Arbeiten, sodass sich die Mitarbeiter auf höherwertige Aufgaben konzentrieren können
LISA war für uns eine unverzichtbare Ressource, die uns dabei half, unsere Umstellungsprozesse sprunghaft zu verbessern und den Druck auf unsere Mitarbeiter zu verringern. Seit der Einführung von LISA haben wir es kontinuierlich weiterentwickelt und verbessert, um unsere Fabrik noch intelligenter und effizienter zu machen.
— Martin Stefan, Leiter Werksintegration, Flex Althofen