
Im Auftrag eines führenden Cloud Infrastrukturanbieter, unser Team in Penang, Malaysia baut Leiterplattenbaugruppen (PCBA) die Cloud Computing ermöglichen. Diese Baugruppen dienen als Gateway zur Cloud für Server und andere Computergeräte. Jede achte Online-Interaktion verläuft über eine von uns erstellte PCBA!
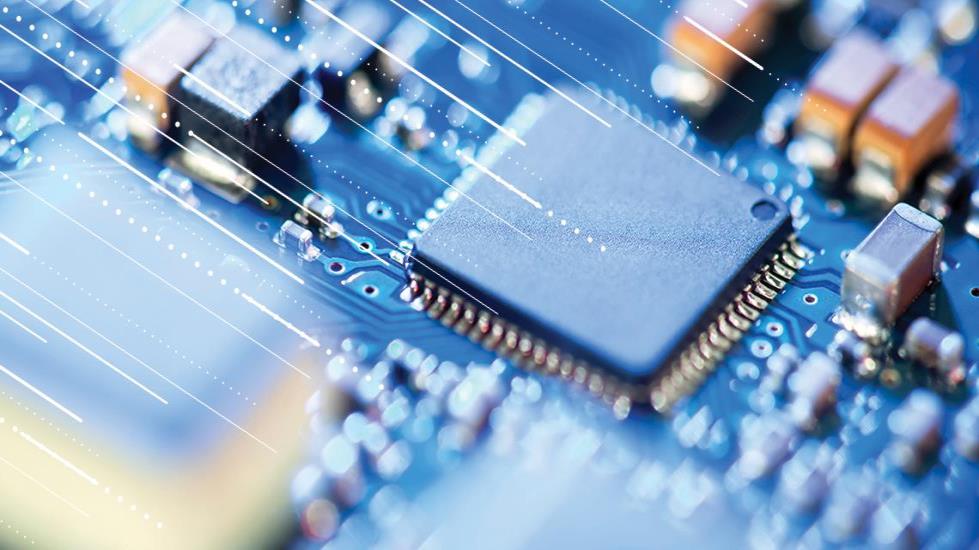
Die Herausforderungen
Wir waren über einen längeren Zeitraum hinweg mit erheblichen Ressourcen- und Produktionsproblemen aufgrund von COVID-19 konfrontiert.
März–Juni 2020
In Kombination mit einem früheren Rückstand verzeichnete unser Kunde zu Beginn von COVID-19 einen Anstieg der Nachfrage nach PCBA-Produkten. Der Online-Verkehr nahm zu, da die Menschen arbeiteten, einkauften, Kontakte knüpften und Unterhaltung über ihre angeschlossenen Geräte streamten.
In dieser Zeit verhängte China einen Lockdown und die Rohstoffe wurden knapp. Unser Produktionsstandort in Penang erhält viele Rohteile des Kunden aus China. Wir mussten die Materialknappheit sorgfältig bewältigen, um sicherzustellen, dass wir die Nachfrage befriedigen konnten.
Gleichzeitig ordnete die malaysische Regierung einen „teilweisen Lockdown“ an, um die Ausbreitung von COVID-19 einzudämmen. Infolgedessen mussten alle Unternehmen mit Ausnahme derjenigen in kritischen Dienstleistungs- und Industriezweigen ihren Betrieb einstellen.
Juli–September 2020
Im Juli 2020 musste unser Kunde dringend 50% mehr PCBA innerhalb von nur vier Wochen liefern. Um dieses Ziel zu erreichen, mussten wir eine beispiellose Skalierung erreichen.
Die Lösung
März–Juni 2020
Drei Tage nach der angeordneten Sperrung erhielt unser Team in Penang die Genehmigung der Regierung, die Produktion dieser Güter schrittweise wieder aufzunehmen – sie wurden als lebenswichtig anerkannt und wir konnten unseren Plan zur Gewährleistung der Sicherheit unserer Mitarbeiter erfolgreich unter Beweis stellen. Zunächst wurde der Betrieb mit einer Kapazität von 15% wieder aufgenommen; im Mai hatten wir die Erlaubnis, die Kapazität auf 50% zu erhöhen. Einen Monat später konnten wir die Kapazität von 100% wieder erreichen und gleichzeitig eine sichere Umgebung für unsere Mitarbeiter aufrechterhalten.
Als die Produktion wieder aufgenommen wurde, änderten wir unseren Herstellungsansatz. Anstatt uns auf die bestehenden „One-Piece-Flow“-Abläufe zu verlassen, was vor COVID-19 optimal war, haben wir unseren Herstellungsprozess neu konfiguriert. Wir haben die Produktfamilien als „Inseln“ verteilt, um den nötigen Platz zu schaffen, damit unsere Teams einen sicheren Abstand halten können.
Das „Insel“-Konzept sorgte für einen nahtlosen Produktfluss und führte zu einer Effizienzsteigerung. Diese Verbesserung fiel mit der Abschwächung der Rohstoffknappheit zusammen und unsere Teams an vorderster Front konnten die verlorene Zeit schnell wettmachen und den Nachfrageschub bewältigen.
Juli–September 2020
Um sicherzustellen, dass wir den neuen Volumenanforderungen des Kunden gerecht werden, hat unser Team in Penang unsere Mitarbeiter in Zhuhai, China, herangezogen, um einen zweiten Fabrikstandort zu qualifizieren und die aktuellen Produktionskapazitäten zu erweitern.
Das Team aus Penang trat in Aktion und begleitete unsere Zhuhai-Kollegen zu einem erfolgreichen Start. Dabei handelte es sich um eine „virtuelle Qualifizierung“, bei der wir demonstrierten, wie jeder Qualitätsindikator erfüllt werden würde. Folglich musste der Kunde kein persönliches Audit durchführen, was durch die Verkürzung des Fabrikqualifizierungsprozesses wertvolle Zeit sparte.
Obwohl das Zhuhai-Team Erfahrung in der Herstellung der Baugruppen hatte, beschleunigte unser Penang-Team seine Lernkurve, indem es ihnen Folgendes zur Verfügung stellte:
- Gründliche Ausbildung und Stammeswissenstransfer
- Umfangreiche Unterstützung bei der Produktqualifizierung
- Ständige Fortschrittsüberprüfungen über mehrere Schichten hinweg; Durch dieses Versehen konnte der Scout-Aufbau des Zhuhai-Teams nahezu perfekt sein
Erfolgsfaktoren:
- Das Penang-Team unterstützte seine Zhuhai-Kollegen schnell bei der Qualifizierung von Werkzeugen und Prozessen. Die Teammitglieder von Penang nahmen schnell Anpassungen an den Maschinenplattformen vor und stellten gleichzeitig schnell technische Daten und Dokumentation bereit.
- Unser Penang-Team lokalisierte außerdem die Produktprofile des Kunden und passte sie an die Produktionsumgebung und -standards von Zhuhai an, wodurch der Onramp-Prozess beschleunigt wurde. Es war das über viele Jahre hinweg entwickelte Produktwissen unserer Penang-Gruppe, das es dem Zhuhai-Team ermöglichte, so schnell aufzusteigen.
- Bei den Wissenstransfers und Übergaben ging es nicht einfach darum, die Parameter des Penang-Teams zu nutzen. Es erforderte den Einsatz fundierter Fachkenntnisse, eine schnelle, disziplinierte Ausführung und die Zusammenarbeit der Ingenieure aus Penang mit dem Zhuhai-Team, um die richtigen „Einstellungen“ zu entwickeln, die für eine Vielzahl von Variablen funktionierten.
Die Ergebnisse
Unser Standort in Zhuhai hat seine erste PCBA in nur vier Wochen qualifiziert – eine Rekordzeit und eine unglaubliche Leistung.
Die Teamarbeit und der gemeinsame Wert, „alles zu tun, was nötig ist“, ermöglichten die einwandfreie Ausführung für unseren Kunden.
Wir haben zwischen Juni und September mehr als eine Million Baugruppen an den Kunden ausgeliefert, ein Rekordvolumen in einem Quartal in unserer 20-jährigen Partnerschaft – und das unter eingeschränkten Bedingungen.
Trotz des Lockdowns und der reduzierten Kapazität lieferte unser Team in Penang weiterhin außergewöhnlichen Service mit Einfallsreichtum, Engagement und vorausschauendem Denken.