
Die Fertigung ist eine komplexe Branche, die in einer Welt agiert, die immer komplizierter wird. In der schnelllebigen, globalen Geschäftslandschaft von heute kann es verlockend sein, sich auf veraltete Betriebsweisen zu verlassen, die in der Vergangenheit funktioniert haben. Die vielen Störungen und Herausforderungen der letzten Jahre – darunter eine globale Pandemie, Komponentenknappheit, geopolitische Unruhen und ein anhaltender Kampf um Talente – haben jedoch deutlich gemacht, dass wir nicht auf dem gleichen Weg bleiben können. Wenn Unternehmen Teil der nächsten Ära der Fertigung sein wollen, sollten sie Geschäftskontinuität und Ausfallsicherheit in den Vordergrund stellen. Produktionsökosysteme müssen anpassungsfähig sein, um zu überleben und zu gedeihen.
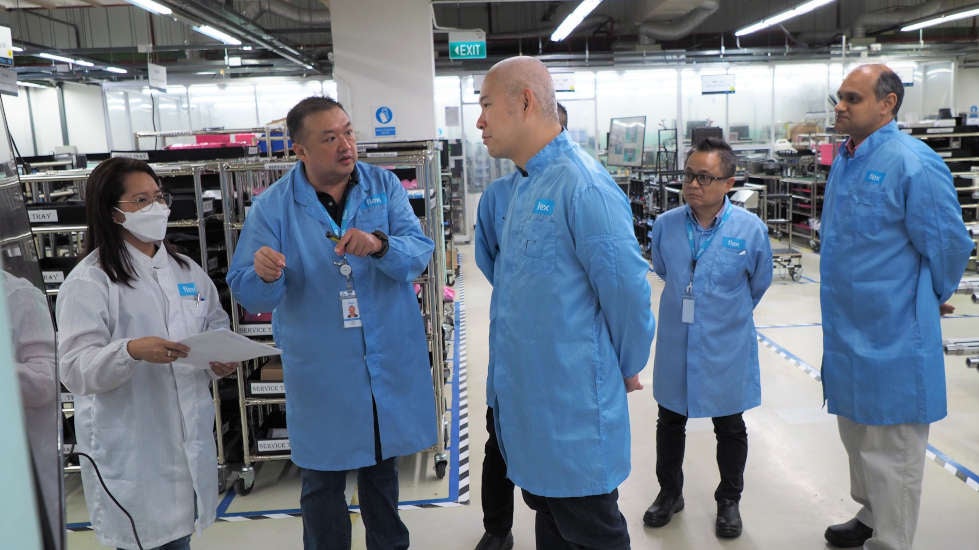
Obwohl es unmöglich ist, jedes zukünftige Ereignis vorherzusagen, können wir das Risiko mindern, indem wir ein robustes Toolkit aufbauen, das es uns ermöglicht, bei neuen Störungen schnell und effektiv zu reagieren, uns neu zu kalibrieren und wiederherzustellen. Aufgrund meiner über 30-jährigen Erfahrung in dieser Branche fordere ich alle Unternehmen dazu auf, Ausfallsicherheit an die erste Stelle zu setzen. Wir können Stürme besser überstehen und wettbewerbsfähig bleiben, wenn wir fortschrittliche Technologien einführen, Prozesse und Arbeitsabläufe optimieren und in eine starke Mitarbeiterbasis investieren.
Umgestaltung der Fabrik mit fortschrittlicher Technologie
In einer zunehmend digitalen Welt müssen Hersteller Industrie 4.0 (I4.0)-Technologien und -Lösungen wie Automatisierung, Simulation und maschinelle Intelligenz (MI) proaktiv implementieren. Eine aktuelle Umfrage von MIT Machine Intelligence for Manufacturing and Operations (MIMO) und McKinsey and Company unter 100 leistungsstarken Unternehmen ergab, dass „insgesamt diejenigen, die die größten Gewinne aus digitalen Technologien erzielten, über eine starke Governance, Bereitstellung, Partnerschaften, MI-geschulte Mitarbeiter verfügten.“ und Datenverfügbarkeit. Sie auch gaben bis zu 60 Prozent mehr für maschinelles Lernen aus als ihre Konkurrenten.“
Ja, diese Unternehmen geben möglicherweise 60 Prozent mehr als ihre Konkurrenten für bestimmte Technologien aus, aber das kann zu optimierten Fertigungslinien, weniger Abfall und einer besseren Sichtbarkeit im Produktlebenszyklus führen. Um den größtmöglichen Nutzen aus diesen I4.0-Implementierungen zu ziehen, müssen sich Unternehmen voll und ganz auf den Prozess einlassen und nicht nur in die Technologie, sondern auch in die Schulung und Entwicklung der Belegschaft investieren. Der Weg nach vorne wird für jedes Unternehmen anders aussehen, aber es besteht immer die Möglichkeit, Technologie zu nutzen, um die Produktivität zu steigern, die Wettbewerbsfähigkeit zu steigern und die Ausfallsicherheit zu ermöglichen.
Beispielsweise könnten sich Hersteller komplexer, teurerer Produkte mit längerem Lebenszyklus – etwa Automobil- und Medizingeräte – dafür entscheiden, in hochspezialisierte Automatisierungslösungen zu investieren, um ihre Produktlinien zu optimieren. Andererseits kann ein Hersteller mit einem hohen Mix an Konsumgütern von der „Vanilla-Automatisierung“ profitieren, d. In beiden Fällen bieten Industrie 4.0-Technologien einen Wettbewerbsvorteil; Es geht lediglich darum, Ihr Unternehmen gut genug zu verstehen, um die effektivste Lösung zu ermitteln.
Darüber hinaus profitieren Hersteller durch Investitionen in die IT-Infrastruktur, die die Datenerfassung und -freigabe über den gesamten Produktlebenszyklus hinweg ermöglicht, von besseren Erkenntnissen für die Produktionslinien- und Lieferkettenplanung. Mit der Datenarchitektur, die jeden Teil des Produktlebenszyklus verbindet – von der Planung über die Produktion und Lagerung bis hin zur Auslieferung und dem Aftermarket – werden Fabriken der Zukunft in die Lage versetzt, störende Ereignisse besser zu bewältigen und mit der nötigen Agilität und Zuversicht zu handeln, um sich von Rückschlägen zu erholen. Es wird uns auch dabei helfen, Wachstumschancen und neue Wege zu erkennen, um wettbewerbsfähiger zu sein und den Verbrauchern mehr Bindung zu verleihen.
Ein aktueller Artikel im Harvard Business Review unterstützt diese Position: „Analytics kann beispielsweise Mitgliedern der Lieferkette dabei helfen, gemeinsame Teile über Produktlinien hinweg zu identifizieren und optimale Puffer zu entwerfen.“ Digitale Zwillinge – digitale Modelle der Lieferkette – können nachgelagerte Werke schneller auf vorgelagerte Störungen aufmerksam machen, sodass sie die Puffer schneller nutzen können.“
Suche nach Möglichkeiten zur Rationalisierung von Prozessen und Produktionslinien
Fabriken der Zukunft erfordern einen starken Fokus auf Prozess-Know-how und eine Kultur der kontinuierlichen Verbesserung. Erwerben Industrie 4.0-Technologien ist nur der erste Schritt auf der Reise; Unternehmen müssen bei der Umsetzung diszipliniert sein und Six Sigma- und Lean-Manufacturing-Prinzipien anwenden, um operative Exzellenz zu erreichen. Bei Flex pflegen wir eine Kultur der kontinuierlichen Verbesserung durch die Anwendung dieser Grundsätze an unseren Standorten. Im Jahr 2022 erhielten beide unsere Standorte in Tczew, Polen und Pelabuhan Tanjung Pelepas, Malaysia Manufacturing Excellence Awards für Lean-Innovation durch die Association of Manufacturing Excellence.
Wenn Sie Prozess-Know-how und Verbesserungspraktiken außer Acht lassen, zahlen Sie möglicherweise einen hohen Preis. Wenn Technologieimplementierungen überstürzt oder schlampig durchgeführt werden, stehen den Unternehmen unter Umständen ungenutzte Maschinen, nicht ausgelastete Softwareplattformen oder Produkte von schlechter Qualität zur Verfügung. Stellen Sie sich einen Hersteller vor, der einen manuellen Inspektionsprozess automatisieren möchte, ohne zuvor sorgfältig die Pass/Fail-Kriterien zu definieren. Es ist wahrscheinlich, dass das Unternehmen am Ende zu viel Ausschuss und höhere Stückkosten hat oder ein Produkt von minderer Qualität erhält, was dem Ruf der Marke und der Kundentreue schadet.
Menschen vor allem wertschätzen
Industrie 4.0-Technologien werden dazu beitragen, die Fabriken der Zukunft zu verändern, aber ich würde es versäumen, die wichtigste Zutat außer Acht zu lassen – die Menschen, die die Fertigungsindustrie zu etwas Außergewöhnlichem machen. Der langfristige Erfolg und die Widerstandsfähigkeit unserer Branche hängen von unserer Fähigkeit ab, zielstrebige Innovatoren, Problemlöser und Macher einzustellen und zu halten, die uns in die nächste Ära der Fertigung führen.
Dies bedeutet, eine Kultur der Zusammenarbeit und zielgerichteten Umsetzung zu schaffen. Es erfordert auch, unseren Mitarbeitern Entwicklungsmöglichkeiten zu bieten, damit sie weiter lernen, sich weiterentwickeln und die fortschrittlichen Technologien nutzen können, die ihre Arbeit sicherer und angenehmer machen. Dies ist ein entscheidender Bereich, wenn Unternehmen auch in Zukunft widerstandsfähig und wettbewerbsfähig bleiben wollen. Tatsächlich zeigen Untersuchungen von McKinsey and Company, dass etwa 45 Prozent der Unternehmen rechnen in den nächsten fünf Jahren mit Qualifikationslücken. Ohne Investitionen in die Entwicklung von Fähigkeiten und Schulungen geraten die Unternehmen ins Hintertreffen.
Beispielsweise haben wir das Capability Acceleration Program bei Flex implementiert, um Mitarbeiter in den USA und auf der ganzen Welt in einem breiten Spektrum von Disziplinen und Fähigkeiten im Zusammenhang mit Industrie 4.0 zu schulen. Die Kurse behandeln Themen wie Automatisierung, Simulation für die zukünftige Modellierung, erweiterte Realität und mehr. Seit 2007 wurden über 18.000 Flex-Mitarbeiter im Rahmen dieses Programms geschult.
Im Produktionsalltag müssen wir auch an die Sicherung der Kapazitäten denken, um nach einer Störung die volle Produktion wieder hochfahren zu können. Beispielsweise machen Hersteller angesichts von Bauteilknappheit manchmal den Fehler, die Belegschaft zu reduzieren, weil sie derzeit über weniger oder weniger optimierte Produktionslinien verfügen.
Oftmals ist es klüger, die Arbeiter dafür zu bezahlen, dass sie im Personal bleiben, bis die Produktion mit voller Kapazität weiterlaufen kann. Menschen sind im Herstellungsprozess sehr wichtig, insbesondere heute, wo viele Länder mit Personalproblemen konfrontiert sind. In der Zwischenzeit können diese Arbeitskräfte auch eingesetzt werden, um vorübergehend andere Fabriklinien oder andere Bereiche des Produktionsökosystems zu unterstützen.
Dadurch können Hersteller flexibel reagieren, wenn Komponenten wieder aufgefüllt werden oder die Nachfrage steigt. In diesem Fall ist die Aufrechterhaltung der Beschäftigung der Mitarbeiter auch während der Ausfallzeiten ein strategischer Aspekt der Resilienz, der den hohen Kosten- und Zeitaufwand für die Neueinstellung und Schulung neuer Mitarbeiter berücksichtigt.
Resilienz steht für alle an erster Stelle
Wir wissen, dass die Zukunft viele Unbekannte bereithält, aber Unternehmen können sich darauf vorbereiten, indem sie in die richtigen Technologien, Prozesse und Mitarbeiter investieren, um echte organisatorische Widerstandsfähigkeit zu erreichen.
Letztendlich muss jedes Unternehmen seinen eigenen Weg vorgeben und die Strategie und Lösungen festlegen, die für seine Anforderungen am besten geeignet sind. Wenn Sie heute einen zukunftsorientierten und menschenzentrierten Ansatz verfolgen, brauchen Sie keine Angst vor Veränderungen zu haben. Stattdessen können Sie alle Innovationen und Chancen nutzen, die eine neue Ära in der Fertigung mit sich bringt.