
Hintergrund
Ein führendes Unternehmen für medizinische Geräte hat Flex für die Herstellung seines Klasse-II-Diabetesprodukts ausgewählt. In den Vereinigten Staaten bezieht sich die Bezeichnung als Medizinprodukt der Klasse II auf Geräte mit einem mäßigen bis hohen Risiko für den Patienten und/oder Benutzer. Mehr als 40 Prozent der Medizinprodukte fallen in diese Kategorie. Sie erfordern höchste Zuverlässigkeit, da Fehler oder Probleme in der Design- oder Herstellungsprozess könnte Patienten gefährden.
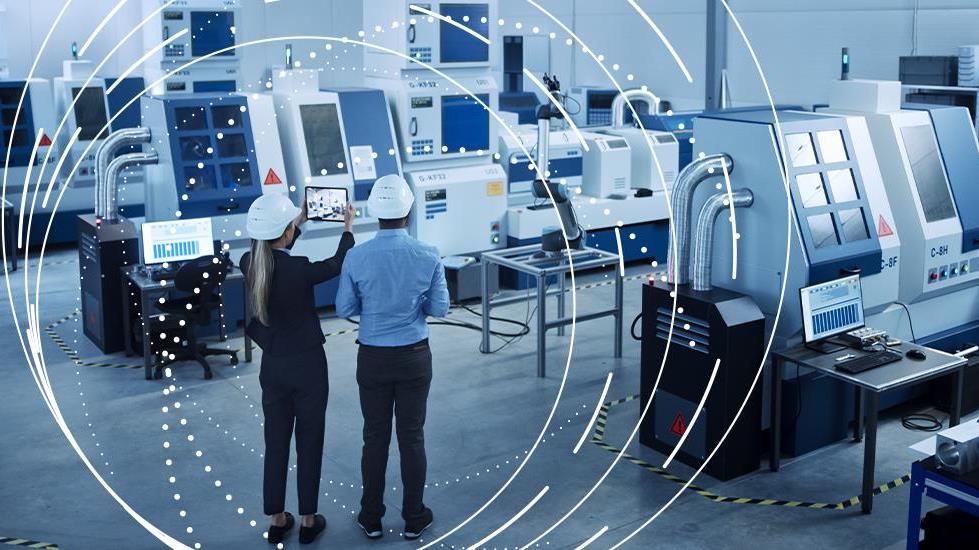
Die Etablierung konformer Herstellungsprozesse für Medizinprodukte kann aufgrund der damit verbundenen strengen Leistungs-, Zuverlässigkeits- und Sicherheitsanforderungen Jahre dauern. Darüber hinaus erfordert jede Änderung dieser Prozesse eine erneute Validierung, Dokumentation und erneute Einreichung bei Regulierungsausschüssen, ein zeitaufwändiger und kostspieliger Prozess, der zu Verzögerungen führen kann. Es kann für viele eine Herausforderung sein, all diese Überlegungen und Prioritäten unter einen Hut zu bringen Hersteller medizinischer Geräte um Prozesse für mehr Agilität und Ausfallsicherheit zu rationalisieren und gleichzeitig alle gesetzlichen Anforderungen zu erfüllen.
Angesichts der hohen Bedeutung des Patientenwohls und der Notwendigkeit einer präzisen Planung und Prognose ist die Herstellung medizinischer Geräte ein idealer Kandidat für Simulationstechnologien, die softwarebasierte Umgebungen zur Optimierung von Prozessen nutzen. Eine dieser Techniken, die diskrete Ereignissimulation (DES), modelliert den Betrieb eines realen Systems als eine Folge diskreter Ereignisse. Es ermöglicht uns, die notwendigen relevanten Montage-, Test- und Versandprozesse sicher und genau zu modellieren, zu simulieren und zu analysieren.
DES beschleunigt die Markteinführung und senkt die Kosten erheblich, indem es uns ermöglicht:
- Gestalten Sie einen effizienten Personen- und Materialfluss
- Sagen Sie Erträge genauer voraus
- Reduzieren Sie den Lagerbestand
- Erhöhen Sie den Durchsatz
Herausforderung
Als sich die Gesundheitsbranche an die dringenden Bedürfnisse der COVID-19-Pandemie anpasste, mussten auch medizinische Fachkräfte umstellen werden widerstandsfähiger damit sie weiterhin andere wichtige Anforderungen im Gesundheitswesen erfüllen können. Wir mussten unserem Kunden helfen, die Entwicklung eines Klasse-II-Diabetesprodukts zu beschleunigen und zu optimieren, um Geschwindigkeit, Qualität und Zuverlässigkeit sicherzustellen und gleichzeitig die Produktion zu steigern und das Risiko angesichts der anhaltenden Herausforderungen einer globalen Pandemie zu minimieren.
Lösung: Optimieren Sie die Fertigung mithilfe von DES, um einen digitalen Zwilling der Fabrikhalle zu erstellen.
Mit dieser virtuellen Darstellung unseres komplexen Produktionssystems haben wir verschiedene Szenarien getestet und Erkenntnisse zu Optimierungstaktiken gewonnen.
Zuerst importierten wir Darstellungen der Produktionsanlagen, wie Ausrüstung, Layout und Personal, in die DES-Software, um den physischen Produktionsprozess nachzuahmen. Wir haben auch analysiert, wie die Ausrüstung in der Umgebung mit anderen Geräten, Personen, Materialien und anderen Objekten zusammenhängt. Dies lieferte eine Grundlage für den Prozessablauf.
Nachdem der Prozessablauf eingerichtet war, haben wir dann relevante Daten geladen und sie dem entsprechenden Asset zugeordnet. Erstellen eines digitalen Zwillings unseres Fabrikbetriebs. Dies ermöglichte es uns, Prozesse zu simulieren, ohne Geräte oder Materialien aufzuwenden, und Hunderttausende „Was-wäre-wenn“-Szenarien zu durchlaufen. Nach Abschluss der Tests überprüften unsere Geschäfts- und Technikmitarbeiter gemeinsam mit unseren Simulationsexperten die Ergebnisse zur weiteren Optimierung.
Wir haben uns auf mehrere Schlüsseldimensionen konzentriert, darunter:
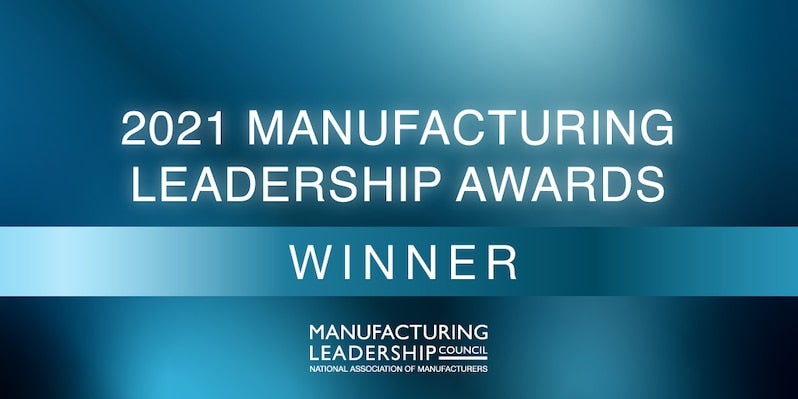
- Ertragssteigerung
- Verwendung von Einkaufswagen zur Beseitigung von Engpässen bei Mehrwertprozessen
- Bewertung des Masterplans zur Steigerung der Auslieferung von 5,5 Millionen auf 8,1 Millionen Einheiten pro Quartal
- Optimierung der Arbeitsauftragsgrößen, um das Material in der jeweiligen Einheit zu verbrauchen
Ergebnisse
Ohne Simulation hätte dieser Testprozess mindestens drei Monate länger gedauert. Aber unser DES-Tool ermöglichte es uns, unsere Optimierungsanalyse in nur drei Wochen abzuschließen, sodass unser Kunde das Produkt schneller auf den Markt bringen konnte. Das hat unserem Kunden Zeit und Geld gespart. Außerdem wurde das Verfahren getestet, um sicherzustellen, dass ein zuverlässiges Produkt entsteht, ein entscheidender Erfolgsfaktor für Medizinprodukte der Klasse II. Durch die Nutzung unserer Simulationskompetenz zur Optimierung von Produktionsprozessen haben wir unserem Kunden geholfen, einen erheblichen ROI zu erzielen.
Beispielsweise können mehr Karren verwendet werden, um Material und unfertige Produkte durch die Fabrik zu transportieren Wertschöpfungsprozesse eine höhere Prozesseffizienz eingeführt. Ohne die Durchführung einer Simulation hätten wir Carts nicht als Lösung identifiziert, um potenzielle Engpässe zu beseitigen und eine größere Ausfallsicherheit zu erreichen.
Große Effizienzgewinne inklusive
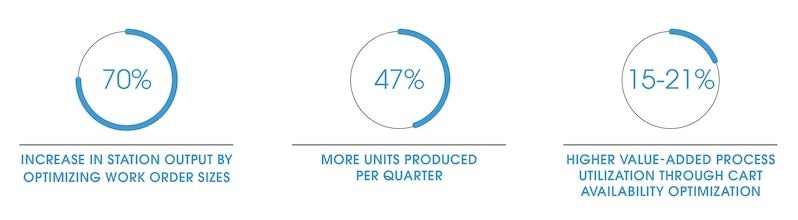