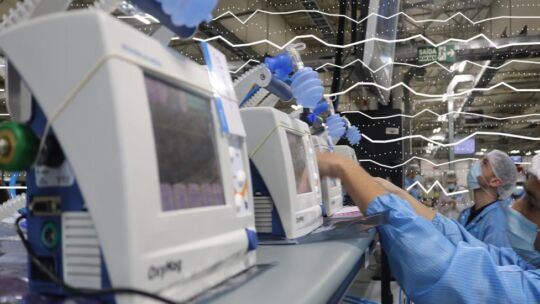
Die Herausforderung
Als COVID-19 im Jahr 2020 auf der ganzen Welt wütete, füllten sich die Intensivstationen mit Patienten, die schwer an dem Virus erkrankt waren.
Die Intensivstation ist die letzte Verteidigungslinie. Dort werden die schwerstkranken Patienten behandelt. Manche bekommen Sauerstoff, damit sie atmen können, während andere an Beatmungsgeräte angeschlossen werden, die ihnen das Atmen abnehmen. Alle bekommen Medikamente, um die Symptome zu lindern.
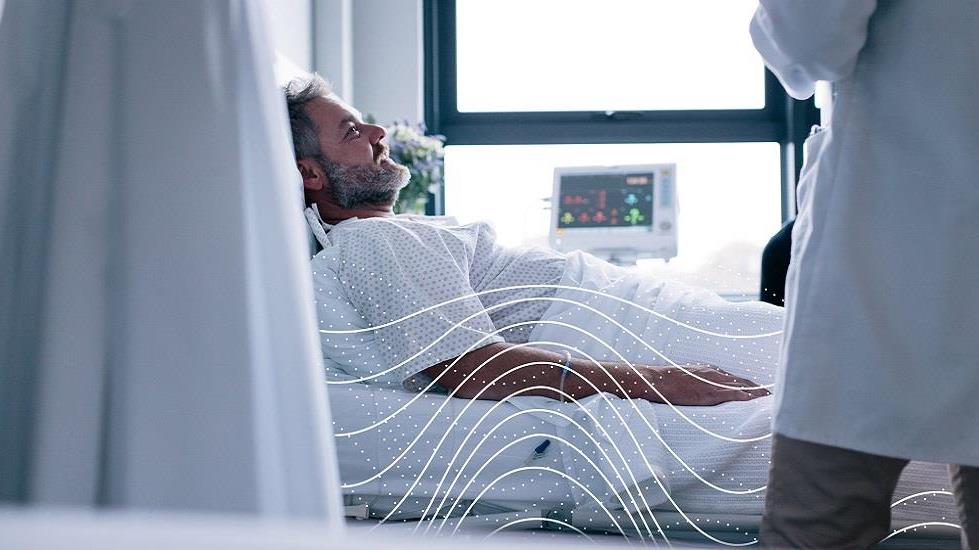
Das Medikament wird normalerweise über eine Infusionspumpe verabreicht – ein medizinische Ausrüstung die Flüssigkeiten in kontrollierten Mengen in den Körper eines Patienten abgibt. Diese mechanischen und programmierbaren Pumpen können größere Mengen an Medikamenten abgeben als andere Methoden wie eine Spritze oder eine einfache Infusion, bei der die Schwerkraft zur Steuerung des Flusses genutzt wird.
Infusionspumpen bieten die Flexibilität, bestimmte Medikamentenmengen zu festgelegten Zeiten automatisch und präzise zu verabreichen. Da jede Pumpe ein einzelnes Medikament abgibt, benötigen manche Patienten mehrere Pumpen gleichzeitig.
Als die Intensivstationen der Krankenhäuser mit COVID-19-Patienten überfüllt waren, gingen die Vorräte an Infusionspumpen schnell zur Neige. Die Lieferanten erhielten eine Flut von Bestellungen und der Druck, mehr zu produzieren, stieg. Unser Standort im rumänischen Timisoara produzierte bereits seit vielen Jahren Infusionspumpen. Das Team dort war in der Lage, die Produktion um bis zu 20–30 Prozent zu steigern, um auf die Nachfragespitze des Kunden zu reagieren.
Dieses Mal musste das Team jedoch fünfmal so viele Pumpen herstellen, um die Nachfrage zu decken. Und zwar schnell, denn COVID zeigte keine Anzeichen einer Abschwächung. Krankenhäuser und Patienten warteten.
Die Produktionslinien sind nicht in der Lage, das Fünffache ihrer normalen Leistung zu produzieren. Die Skalierung stellte eine weitere Hürde dar, da die Pandemie dazu geführt hatte, dass die Lieferketten entweder blockiert, unterbrochen oder geschlossen waren. Schon ein einziges fehlendes Teil könnte bedeuten, dass die Infusionspumpen nicht hergestellt werden konnten.
Die Lösung
Der erste Schritt zur Produktionssteigerung bestand darin, die Anzahl der Schichten an den bestehenden Produktionslinien zu erhöhen, um sofort größere Mengen produzieren und ausliefern zu können. Parallel dazu wurde Platz in der Fabrik geschaffen und mit dem Bau der zusätzlichen Produktionslinien begonnen.
Es wurden neue Produktionsmitarbeiter eingestellt und einige vorhandene Mitarbeiter aus anderen Bereichen der Fabrik abgezogen. Beide Gruppen wurden in ein intensives Schulungsprogramm eingebunden, um sie schnell auf den neuesten Stand zu bringen. Druck hin oder her, die Qualität des Produkts musste auf höchstem Niveau bleiben.
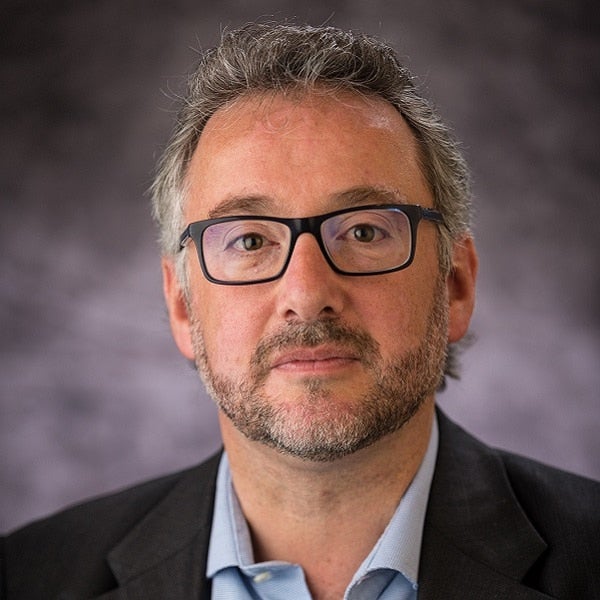
Kein Medizinunternehmen würde Kompromisse bei der Qualität dulden. Qualität ist eine Selbstverständlichkeit. Darüber reden wir nicht einmal. Was auch immer wir in Zukunft liefern, muss dieselbe Qualität haben wie bisher.
— Fabio Rotelli, Account Manager und Senior Director bei Flex
Die wirkliche Herausforderung bestand jedoch in der Versorgung mit den Komponenten, aus denen die Infusionspumpen bestanden. Der Druck durch die dramatisch gestiegene Nachfrage war in der gesamten Lieferkette spürbar. Sowohl unsere Zulieferer als auch die kundengesteuerten Zulieferer mussten ihre Teileproduktion schnell steigern.
Wenn es hart auf hart kommt, kommt es auf die Größe an. Einer der Vorteile eines großer, globaler Hersteller besteht darin, dass einige gängige Komponenten von verschiedenen Lieferanten oder sogar aus verschiedenen Unternehmensbereichen bezogen werden konnten. Während die Nachfrage nach medizinischen Verbrauchsmaterialien und Geräten enorm zunahm, verlangsamte sich die Konjunktur in anderen Bereichen, wodurch Komponenten frei wurden, die in die Produktion von Infusionspumpen einfließen konnten.
Noch mehr erreichen
Ich weiß nicht, wie viele zusätzliche Meilen wir gelaufen sind. In den Nachrichten wurde immer wieder darüber berichtet, wie die Intensivstationen belegt waren. Aber in manchen Fällen fehlte einem vielleicht die nötige Ausrüstung, um den Patienten zu versorgen, selbst wenn man ein Intensivbett hatte.
— Fabio Rotelli
Es gab tägliche Lieferkettenmeetings mit dem Kunden, bei denen wir uns gemeinsam für jede zusätzliche Einheit einsetzten, die wir herstellen konnten.
Die Infusionspumpen verwenden kundenspezifische Komponenten, wie z. B. interne Motoren, die exklusiv für sie gebaut werden. In vielen Fällen liefert nur ein Lieferant eine spezielle Komponente, und für einen kleineren Hersteller könnte eine Nachfrage- oder Engpassherausforderung dieser Größenordnung katastrophale Folgen haben. Jeder Lieferant erhielt Zugang zu unseren globale Lieferketten, sowie die unserer Kunden. Was auch immer sie brauchten, es wurde beschafft.
Um alle Lieferanten im Netzwerk zu motivieren, führten wir gemeinsam mit dem Kunden Schulungen zu dem Produkt durch, für das sie Komponenten lieferten. Viele Lieferanten waren sich nicht bewusst, dass die von ihnen hergestellten Schrauben, Motoren oder anderen Komponenten wichtige Bestandteile im Kampf gegen COVID-19 waren.
Die Störungen und die Komplexität der Lieferkette nahmen zu, da jede Regierung ihre eigenen, einzigartigen Beschränkungen und Vorschriften einführte. Handelsrouten auf der ganzen Welt waren betroffen. Die Verwaltung einer globalen Lieferkette vor diesem Hintergrund einzigartiger und wechselnder Richtlinien kann entmutigend sein, aber Erfahrung und Innovation haben uns geholfen, die Anforderungen des Kunden zu erfüllen.
Ergebnisse
Es wurde alles getan, um der gestiegenen Nachfrage nach diesen lebensrettenden Geräten gerecht zu werden – von der Verkürzung der Produktionsschichtmuster und der Beschleunigung der Lieferketten bis hin zur Wiederverwendung von Komponenten aus anderen Bereichen.
In nur 13 Wochen hatten wir Produktionspersonal eingestellt und geschult, neue Produktionslinien aufgebaut und die Produktion verfünffacht. Die neuen Linien waren voll betriebsbereit, während die Nachfrage nach Infusionspumpen hoch blieb.
Unser System funktionierte, weil wir so viele Bezugsquellen für Ersatzteile hatten. Fabio sagte, dass der Kunde im Laufe der Zeit unter anderem erkannte, dass wir Herausforderungen meistern und liefern können.
Teamarbeit war für den Erfolg dieses Projekts von entscheidender Bedeutung. Ich denke, die beiden Teams haben sich gegenseitig als sehr engagiert erlebt, und das war der Kitt, der dieses Projekt so erfolgreich gemacht hat.
— Fabio Rotelli